A visual factory is one of the most crucial components to organizational success. Have you ever imagined life without visual signages? Think about it: firstly, what would it be like if there were no traffic signals? On the other hand, what if there were no signages to mark big chains like Walmart? It would be impossible to live without these visual displays! Therefore, think about how easy life (and operations) can be inside a workplace that uses visual factory ideas.
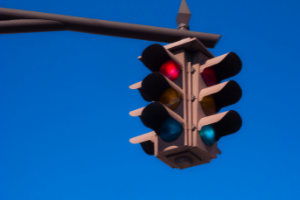
Figure 1 explains the various levels of a visual factory. Firstly, it begins with creating a 5S-compliant workplace. 5S is a good foundation for creating a world-class visual factory! Most importantly, visual signages should aim at making it easy to direct the workforce to improve quality and efficiency in a plant. However, a good-looking plant is just a by-product of 5S and visual factory implementation. It shouldn’t be the goal!
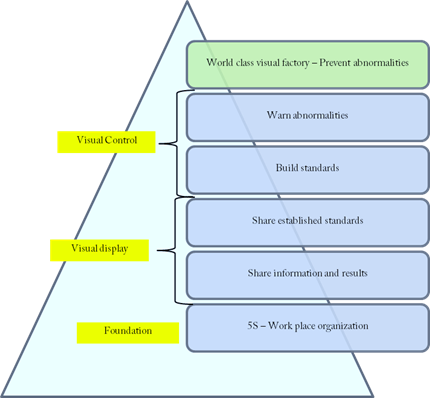
Figure 1: Levels in a visual factory
The table below explains the various levels of a visual factory, along with examples. Standard work is the starting point. In the table below, Andon and Jidoka represent the highest level of the visual factory. Over time, the standards are built into the machine. Hence, they start working as Poka-Yoke.
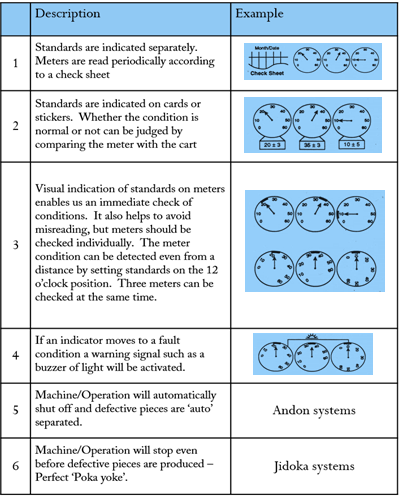
Table: Levels in a visual factory (examples)
Where to apply visual factory concepts?
A visual factory should be applied in factory settings for several reasons. Most importantly, the end goal of a visual factory is to aid productivity, efficiency, and quality achievements. Additionally, it aims to make self-help easy and attainable for a layperson. For instance, find below some aims of visual factory ideas along with relevant examples:
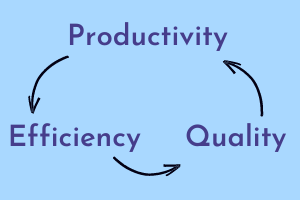
-
Inform
– Performance
– Production status
– Production plans
– Key instructions for the day, week, etc.
-
Direct
– Do’s/ Don’ts
– Work instructions/ SOP/ Standard work
-
Warn
– Andon boards
-
Track
– Production flow stage and quantities
– Skill matrix
– Plan vs. actual status
– Order delivery status
-
Control
– Process and output deviations
– Raw material deviations
– Deviations from standard operating procedures
To succeed, your visual factory and 5S principles should align with the company’s long-term goals. Above all, do not use a visual factory to please customers or to win a competition! This is an absolute no-no. If you follow these principles sincerely, the factory will look appealing in itself. Hence, you won’t need to put in any extra effort!
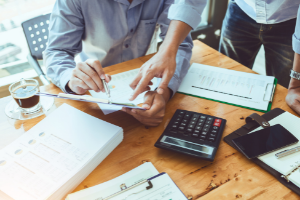