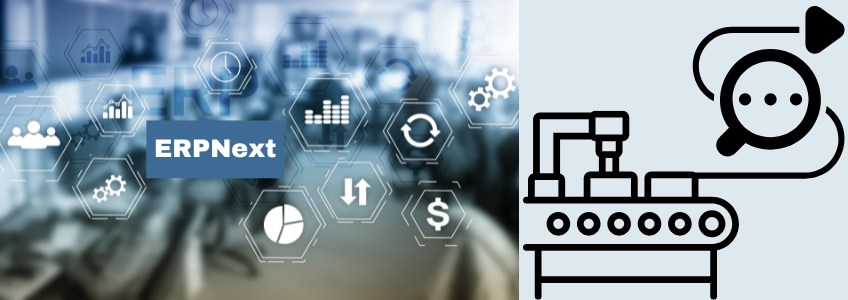
Introduction
In the world of manufacturing, companies often face a significant challenge. This challenge lies in identifying the raw materials used in finished goods (FG) that are rejected by customers. This issue primarily stems from the lack of traceability in raw material batches utilized at different stages of the production process.
Without a robust system to track and trace these batches, manufacturers struggle to pinpoint the root cause of quality issues. This in turn leads to inefficiencies, increased costs, and potential customer dissatisfaction.
The Importance of Raw Material Traceability
In any manufacturing process, especially in industries dealing with chemicals, traceability is critical for:
- Quality Assurance: Ensuring that raw materials meet the required standards.
- Regulatory Compliance: Meeting industry regulations that mandate detailed record-keeping.
- Root Cause Analysis: Quickly identifying issues when a product is rejected.
- Customer Trust: Providing transparency to customers regarding the source and quality of materials.
Without a clear system in place, tracking back the raw materials used in a rejected FG can become a time-consuming and error-prone process. This is where ERPNext becomes a game-changer.
How ERPNext Enhances Traceability
ERPNext, an open-source enterprise resource planning software, offers built-in functionality to manage raw material batches efficiently. Here’s how it addresses the challenges faced by manufacturing companies.
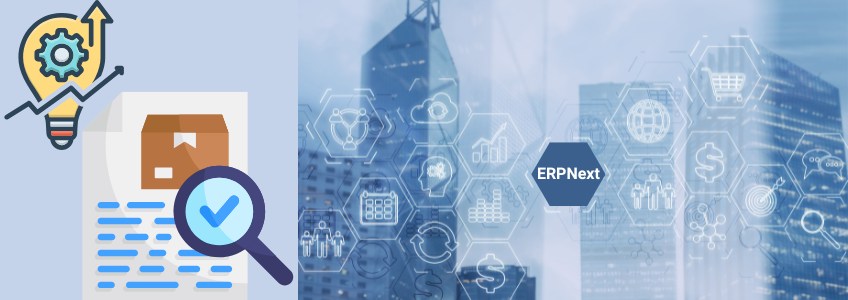
1. Batch-Wise Material Issuance
ERPNext allows manufacturers to issue raw materials batch-wise during production. Each batch is assigned a unique identifier, ensuring that its usage is recorded at every stage of the manufacturing process. This creates a digital trail that can be easily accessed when needed.
2. Backtracking Made Simple
When a customer rejects a finished good, ERPNext’s traceability features make it easy to backtrack through the production stages to identify the raw material batches involved. This reduces the time required to investigate issues and implement corrective actions.
3. Integrated Inventory Management
ERPNext integrates inventory management with batch tracking. This ensures that stock movements, quality checks, and material usage are recorded in real-time, providing a comprehensive view of the production process.
4. Quality Control at Every Stage
With ERPNext, companies can implement quality control checkpoints at various stages of production. The system logs these checks along with batch details, helping to isolate defects and prevent them from reaching customers.
5. Regulatory Compliance Made Easy
ERPNext simplifies compliance with industry regulations by maintaining detailed records of raw material batches, production processes, and quality checks. These records can be readily accessed during audits, saving time and effort.
Conclusion: The Bottom Line
For manufacturing companies, the lack of raw material traceability can lead to significant challenges, including financial losses and damage to customer relationships. Manufacturers can streamline their production processes, ensure compliance, and build trust with their customers by leveraging ERPNext.
ERPNext’s batch management and traceability features provide the transparency and control needed to address these challenges effectively. With its user-friendly interface and powerful capabilities, ERPNext is the ideal solution for manufacturers looking to enhance their operational efficiency and product quality.
Are you ready to revolutionize your manufacturing process using ERPNext? Write to us to achieve similar success!