The final step to making a current state value stream map is Step 9 – to calculate the Value-Added Ratio percentage (VAR). Make sure you go through the first, second, third, fourth, fifth, sixth, seventh and eighth steps before you start reading this article. It’ll help enhance your holistic understanding of the CSVSM process. Here’s a recap of the steps that I recommend you to follow initially while making your CSVSM:
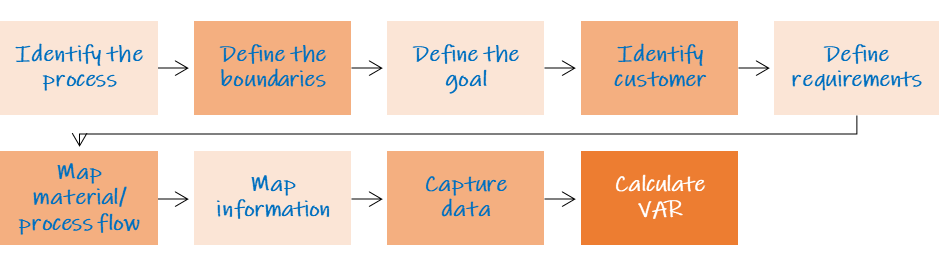
Figure 1 – Steps to construct a CSVSM
Step 9: Calculate VAR (Value-Added Ratio %)
VAR will help you understand the percentage of the time that work undergoes value addition. You will be surprised when you find the value-added ratio for the value stream map you made!
How do we calculate VAR?
Here is an example to calculate the value-added ratio for a current stream value stream map:
- Turnaround time of a file: 8 hours = 28,800 seconds
- VAR: VA time/ Total time = (210/ 28,800) = 0.729%.
- Result: This means that in less than 1% of the time, a file undergoes value-addition.
Do not worry when you look at a meagre figure regarding your VAR. This value is no different from those of the top companies in the world! Looking at your work from the customer’s viewpoint is still not prevalent in the industry. Many are yet to embark on the Lean implementation journey. To know the VAR is just the beginning!

Figure 2 – A completed VSM in IT services
Find below in pictures, how we accomplish value stream activity in a company. Though, our approach to put up a value stream map differs from company to company. Find below one such value stream mapping efforts in pictures with captions.

- Orient the team members on Lean principles and value stream mapping activity. Why this exercise, and how will it help them? Form teams and assign responsibilities.

- After the orientation, go to the shop floor. Walk the process, take a quick tour end-to-end, and write the steps on sticky notes as you walk the steps. Take videos if helpful.
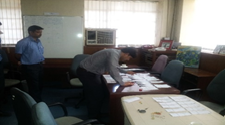
- Put together your observations on the chart paper. Complete a first draft quickly (even if without data) to develop a data collection plan. Visit the steps again – this time for the data collection purpose.

- Involve team members you interacted with during your shop floor visit to put together the value stream map. Remember, it is their process, and their data. Therefore, they must own the information displayed on the map!
Now that you know all the steps to making your current state value stream map, check out how you can use this knowledge while carrying out the Lean principles!