Achieving improvement is just half of the story. The other half is to sustain it! Therefore, amidst implementing the first 4 Ss (‘sort’, ‘set in order’, ‘shine’, and ‘standardize’), the most crucial aspect is to ensure they remain consistent. You must have the necessary systems in place that will sustain 5S in an organization. It involves commitment from everyone in the organization. However, a 5S initiative will fail if it isn’t aligned with the company’s annual goals and objectives.
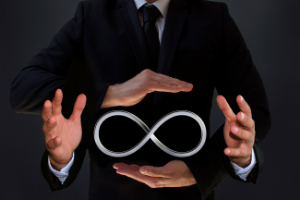
5S is often perceived as a housekeeping practice rather than a ‘way of life’. As a result, it is difficult to sustain the practice. To change this perception, everyone in the company must lead by example. It shouldn’t just be preached. Here are some simple steps involved in sustaining a 5S implementation within an organization:
How do I sustain 5S?
- Firstly, divide the work into small manageable areas.
- Secondly, assign a team leader to each area. Additionally, assign accountabilities and responsibilities.
- Next, carry out cross audits.
- You need to reward and recognize the best 5S areas.
- Furthermore, align the 5Ss with the company’s vision and mission.
- Above all, the leadership should lead by example.
- Create visual storyboards everywhere.
- Train everyone on the 5S principles.
- Make 5S a part of new employee induction.
- Don’t forget to dispose of red-tag items periodically.
- Show commitment to 5S.
- Ensure that you avoid making 5S simply a show for customer visits. On the contrary, people should follow 5S every hour of every day!
- Upgrade 5S to the next level through a visual factory.
- Make sure that all 5S-related communication is made visual. Here’s a picture of a visual factory storyboard:
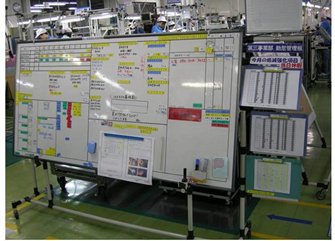
A visual storyboard
Factors behind the lack of 5S sustenance:
- Firstly, 5S isn’t always prioritized.
- Secondly, 5S is perceived as an initiative that doesn’t result in monetary savings. Therefore, there is a lack in both interest and championship from leaders.
- Thirdly, 5S initiatives don’t always align with a company’s annual goals.
- Fourthly, there is often little or no action on red-tag items.
- Fifthly, training ends with training! There are no action plans.
- Sixthly, little to no actions follow on discussed ideas.
- Additionally, a minimal budget is allocated for implementing good practices such as aisles, good storage racks etc. Furthermore, approval takes a long time. By the time it’s received, interest and momentum are both lost.
- Lastly, people consider 5S as nothing more than a ‘make your workplace look good’ initiative.
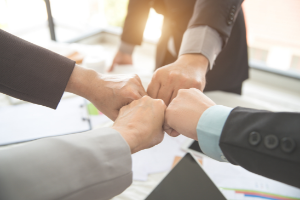
A major change is required in the way people view the functionality of 5S. Above all, leaders need to be involved in the 5S initiative if they want to sustain it. They should implement 5S every day. This will show its prioritization.
Now that you are well-versed in the basics of the 5S approach, make sure you clarify all your 5S doubts before you start implementing it in your workplace!