Sky-Rocketing Productivity in a Factory – A Lean Success Story
To identify and solve a problem in 3 days within a limited budget – these made up the circumstance under which we worked and increased a company’s productivity by 150%!
What sets us apart from contract laborers and other consultants is that our actions are based on the prioritization of a company’s vision, mission, employees, and customers, and a customized approach to Lean measures. We believe these to make up the foundation of Lean thinking. This is precisely the motto that we followed in this case.
The underlying key that we pivot Lean’s seamless integration into an organization’s framework is by ensuring that there is a predetermined process and that the success obtained is measured using numbers.
Here is an account of a factory in which we increased productivity by 150%, and which consequently triggered a change in other branches.
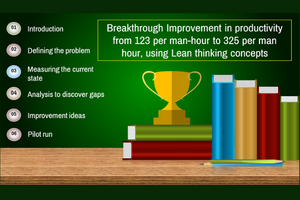
Figure 1: Flow of the Case Study
Defining the Problem
The first step to any Lean story success is to define the problem at hand. The issue, in this case, was the turnaround time of the bank statements. The target turnaround time was 24 hours, starting from the image receipt, all the way up to the posting.
The entire process comprised of the following steps:
- First, the company receives images of bank statements.
- Second, they then print them.
- Third, these are stuffed into envelopes and posted to the customer.
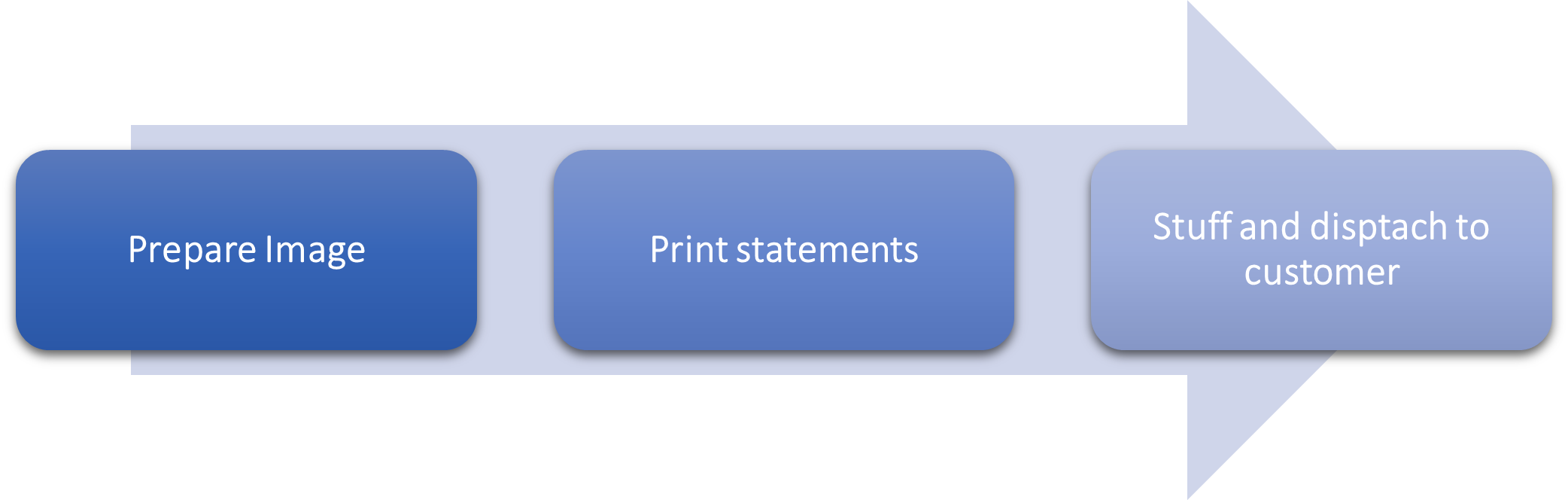
Business Case:
The issue was that the turnaround time was greater than the expected 24 hours! As a result, customers threatened to pull the orders back if the turnaround time did not improve – which focus on primarily credit and debit card statements. Therefore, the bottom line is that if the statements don’t leave on time, it leads to customer complaints and a denial to pay a penalty by citing delayed receipt of the statements.
Goal Statement:
Therefore, to eradicate this problem, the goal statement that was created targeted the reduction of the turnaround time to less than or equal to the ‘expected’ or target hours.
Next, we measured the current state and proposed improvement ideas. To find out more about these steps, keep checking our blog for weekly updates!