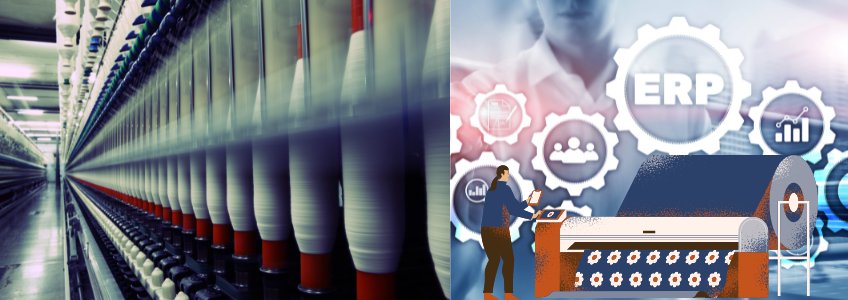
In the textile industry, ensuring accurate product traceability is a formidable challenge. The nature of textile materials, especially yarns, presents unique difficulties. These materials often look indistinguishable from one another, making it hard to track and trace them effectively throughout the production process.
|| 4 minutes read ||
Overcoming Yarn Traceability Challenges: The Problem with Identifying and Tracking Textile Materials
Yarns are the backbone of textile production. They are produced in large volumes and stored in similar-looking beams and logs for further processing, which complicates the task of differentiating them. Each yarn log is associated with a specific batch, and job cards are traditionally used to maintain this identity.
However, job cards can easily be misplaced or lost during production. When this happens, the consequences can be severe. For example, a log from one batch might be mistakenly processed using parameters meant for another batch. This can lead to quality issues, production delays, and increased costs.
How does ERPNext Transform Yarn Traceability?
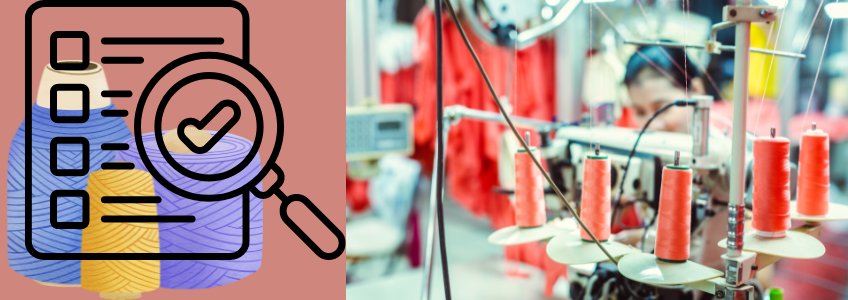
Implementing ERPNext in textile companies offers a robust solution to these traceability challenges. Here’s how ERPNext can transform yarn traceability:
- Accurate Tracking: ERPNext ensures that every log and beam is tracked accurately from the moment the yarn is issued. This system links each log with its respective order number, set number and sort number from the start, making it easier to trace each yarn batch throughout the production process.
- Real-Time Updates: The software provides real-time updates on the status of each log. It shows how many logs are in the Work in Progress (WIP) category and how many have already been processed, offering a clear picture of the production flow.
- Digital Records: ERPNext maintains digital records of each log, mitigating the risks associated with lost or misplaced job cards. Even if a physical job card is lost, the digital trail ensures that traceability remains intact.
- Reduced Errors and Improved Efficiency: By reducing the risk of errors associated with manual tracking, ERPNext enhances the overall efficiency and quality control in the production process. It helps ensure that each batch of yarn is processed correctly, reducing costly mistakes and improving the consistency of the final product.
Conclusion
ERPNext provides a reliable and accurate method for tracking materials in the textile industry. Its advanced tracking capabilities and digital record-keeping significantly reduce the likelihood of any cost-related errors and ensure that every batch of yarn is handled correctly. For textile companies striving to improve their product traceability and overall efficiency, ERPNext offers a compelling solution.
If you are interested to achieve similar success stories, write to us!