Transforming Flour Milling Operations with ERPNext: A Case Study
Industry: Food Processing
Author: Avinash Pallantla
Publish Date: 14 February, 2025
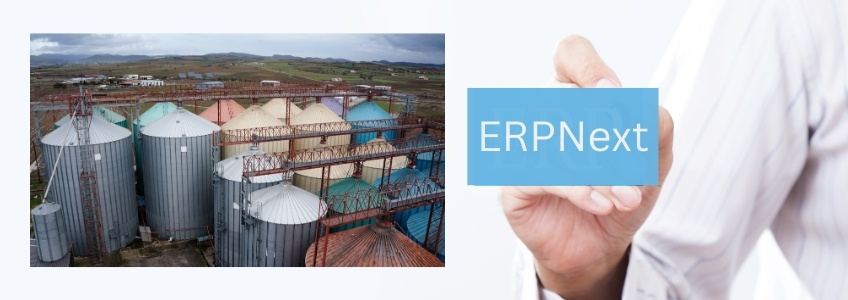
Introduction
Managing a large-scale flour milling operation involves navigating complex challenges. Especially when dealing with inventory, quality control, and production efficiency.
This case study explores how a prominent flour milling company in Hyderabad successfully overcame operational inefficiencies by implementing ERPNext. The company was able to streamline processes and reduce costs with the help of ERPNext. This comprehensive ERP solution also helped them enhance their productivity.
About the Company
The company is one of the largest flour mills in Hyderabad, equipped with a world-class flour milling setup. Catering to the Indian market, the company offers 30-40 different SKUs of atta and maida-related products. Their commitment to quality and innovation has made them a key player in the industry.
Challenges
Despite their market dominance, the company faced several operational hurdles.
- Inventory Management: Tracking inventory accurately at various stages—raw materials, work-in-progress (WIP), and finished goods (FG)—was challenging. Reliance on Excel spreadsheets led to inefficiencies and a lack of real-time visibility.
- Losses from Low-Quality Raw Materials: Inconsistent raw material quality resulted in significant waste, but the company lacked a system to identify and address these issues effectively.
- Inefficient Plant Runtime: Without a robust production planning system, the company struggled to manage plant operations efficiently. This led to higher operational costs and underutilized resources.
Why They Chose ERPNext
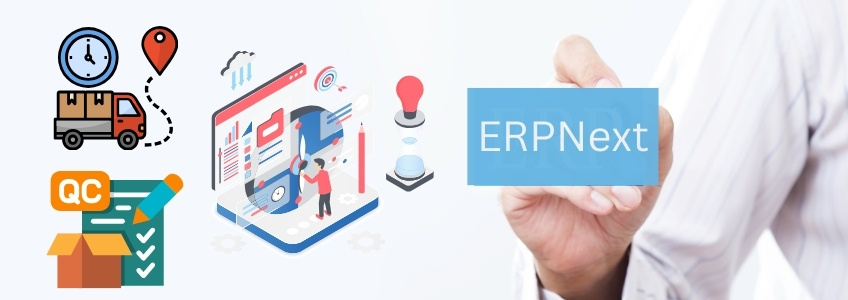
The company decided to implement ERPNext due to its robust and customizable features. It offered:
- Real-time tracking of inventory and production processes.
- Comprehensive quality control mechanisms.
- Efficient production planning tools.
How ERPNext Helped
ERPNext addressed the company’s challenges through the following key improvements.
1. Enhanced Inventory Management
- ERPNext enabled stage-wise inventory tracking, covering raw materials, WIP, and FG.
- The introduction of batch-wise tracking eliminated malpractices and theft, saving the company INR 3-5 lakhs per month.
- With detailed batch records, the company could trace the origin of raw materials and their transformation into finished goods.
2. Improved Quality Control
- The batch-wise tracking system allowed the quality team to identify which batch of raw material generated the highest percentage of waste.
- This transparency enabled the company to raise quality complaints with suppliers and claim reimbursements, resulting in significant cost savings.
3. Optimized Production Planning
- ERPNext’s production planning module provided insights into raw material stock levels and requirements.
- The team could forecast how long the plant could run based on current stock and pending orders.
- Improved planning increased operational efficiency and resource utilization by 15-20%.
Results
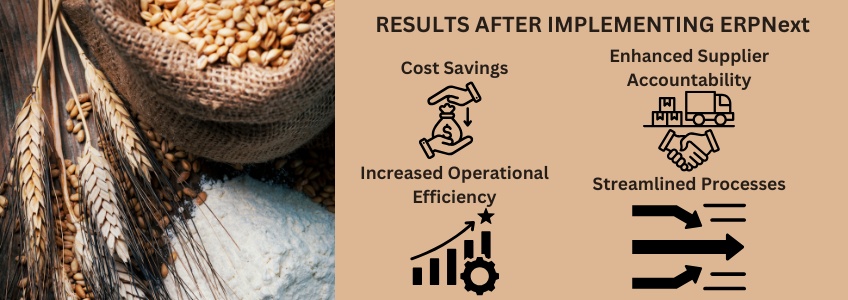
The implementation of ERPNext led to transformative results:
- Cost Savings: Monthly savings of INR 3-5 lakhs through improved inventory management and reduced malpractices.
- Enhanced Supplier Accountability: The ability to claim reimbursements from suppliers for low-quality raw materials.
- Increased Operational Efficiency: A 15-20% improvement in resource utilization and plant runtime efficiency.
- Streamlined Processes: Real-time visibility into inventory and production processes, enabling better decision-making.
Conclusion
Hence, by adopting ERPNext, the flour mill in Hyderabad successfully overcame its operational challenges and established a more efficient, transparent, and cost-effective workflow.
This case study therefore, demonstrates the power of ERP solutions in transforming traditional industries. It also highlights ERPNext as a vital tool for businesses aiming to optimize their operations and stay competitive in today’s market.
If you are interested to achieve similar success stories, write to us!