How ERPNext Transformed Inventory Management for SAC.
Industry: IT Services
Author: Ramanujan KK
Publish Date: 14 February, 2025
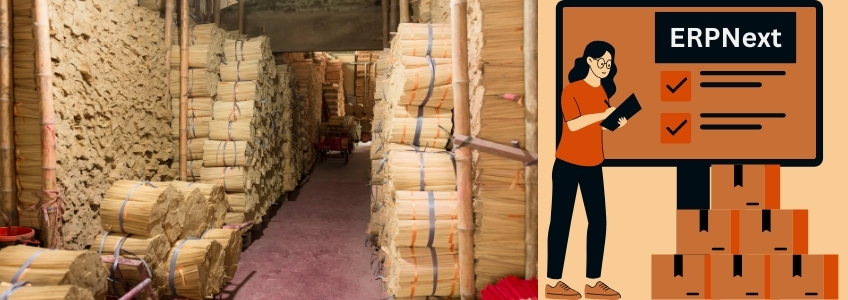
Introduction
This success story is about a leading manufacturer of incense sticks (Agarbathi) manufacturing company, based in Bengaluru, India. The company, known for its high-quality aromatic products, had been growing rapidly, with its production spread across multiple units and warehouses. However, managing inventory efficiently across these locations was becoming increasingly complex.
After implementing ERPNext with customized solutions tailored to their needs, Agarbathi Innovations experienced significant improvements. Their inventory accuracy had improved, stock discrepancies had been reduced, and warehouse operations had also been streamlined.
In this case study, we explore how ERPNext helped Agarbathi Innovations transform its inventory tracking and location management, resulting in measurable improvements.
About the Company
The client company SAC has been a trusted name in the incense stick industry for over 35 years. They have been supplying both domestic and international markets with premium quality Agarbathi and other incense products. With a reputation for consistency and high standards, SAC operates several warehouses across India. As the demand for their products grew, the company expanded its operations, but with this expansion came a series of inventory-related challenges.
The company was struggling with inaccurate stock levels, inefficient warehouse management, and poor tracking of raw materials and finished products across different locations. Their traditional inventory systems, largely based on spreadsheets, were no longer sufficient to handle the complexity of their operations.
The Challenge of Inventory Tracking and Location Management
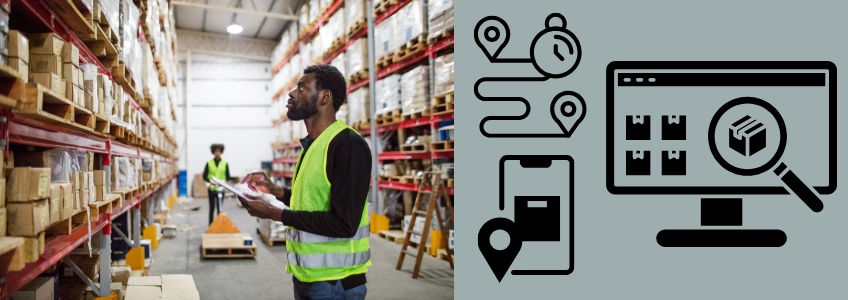
Before implementing ERPNext, SAC faced several challenges related to inventory tracking and location management.
- Lack of Real-Time Inventory Visibility: The company had multiple production units and warehouses, but they could not get real-time visibility into stock levels across locations, leading to frequent stockouts and overstocking.
- Inaccurate Stock Reconciliation: Manual tracking of raw materials and finished goods often led to inventory discrepancies, making stock reconciliation and audits time-consuming and error-prone.
- Inefficient Warehouse Operations: With no system in place for tracking product movement between different locations, warehouse managers struggled to ensure optimal stock levels and manage the flow of goods efficiently.
- Raw Material Tracking: Agarbathi Innovations had difficulty tracking raw materials like bamboo sticks, charcoal powder, and essential oils, leading to delays in production due to stockouts or overstocking.
- Delayed Order Fulfilment: With poor inventory visibility and mismanagement of stock at different locations, order fulfillment was delayed, which impacted customer satisfaction.
Why SAC Chose ERPNext
SAC decided to implement ERPNext due to its robust inventory management features, customizability, and flexibility.
They were looking for a solution that could:
- Provide real-time stock tracking across multiple locations.
- Offer customization for raw material and finished goods inventory management.
- Streamline warehouse operations by automating stock movements and transfers.
- Integrate production processes with inventory, ensuring timely raw material availability.
After evaluating multiple ERP systems, SAC chose ERPNext because of its user-friendly interface, comprehensive features, and strong community support. Additionally, ERPNext’s ability to offer customized inventory management suited their specific needs.
How ERPNext Responded
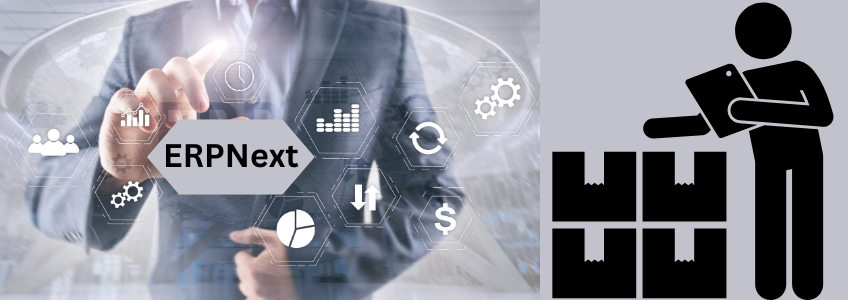
Once SAC implemented ERPNext, we, the team of SKIL Global, worked closely with them to customize the system to meet their specific inventory management needs.
Mentioned below is a detailed description of how we tackled their challenges.
- Multi-Location Inventory Tracking: We customized the Inventory module in ERPNext to enable real-time tracking of stock across multiple warehouses and production units. Each location had its inventory dashboard, making it easier for managers to track stock levels, monitor usage, and plan accordingly.
- Raw Material and Finished Goods Tracking: We customized ERPNext to create inventory categories for raw materials (e.g., bamboo sticks, charcoal powder, essential oils) and finished goods (incense sticks, cones, and other products). The system automatically tracked raw material consumption based on production schedules. This ensured that materials were always available when needed.
- Automated Stock Replenishment: Using ERPNext’s automated alert system, we set up reorder levels for raw materials and finished goods. When inventory reached the minimum threshold, the system automatically triggered purchase orders. This reduced stockouts, maintaining continuous production.
- Inventory Reconciliation: We implemented automated inventory reconciliation processes. This allowed SAC to compare physical stock with the recorded stock in the system. Any discrepancies were flagged for investigation, reducing manual audits and improving inventory accuracy.
- Production and Inventory Integration: ERPNext’s production module was linked directly to inventory. This integration allowed the company to track how much raw material was used in production. In turn, giving them a clear view of the material flow and ensuring that production schedules were aligned with available inventory.
The Results
The improvements were immediate and measurable. Here’s how ERPNext’s customized solution positively impacted SAC’s inventory management:
- 25% Reduction in Stockouts: By implementing real-time inventory tracking and automated stock replenishment, the company reduced stockouts by 25%, ensuring that production lines were never halted due to material shortages.
- 30% Improvement in Inventory Accuracy: Barcode scanning and automated reconciliation processes led to a 30% improvement in inventory accuracy, reducing discrepancies between actual stock and system records.
- 20% Reduction in Overstocking: With automated stock alerts and better visibility, SAC reduced overstocking by 20%, optimizing warehouse space and reducing carrying costs.
- 15% Faster Order Fulfillment: Improved inventory visibility and streamlined warehouse operations resulted in 15% faster order fulfillment times, allowing the company to meet customer demands more efficiently.
- 40% Reduction in Manual Effort for Stock Audits: With real-time inventory updates and automated reconciliation, stock audits became 40% faster, saving both time and labor costs.
- 50% Improvement in Raw Material Utilization: Automated tracking of raw materials reduced waste and improved the overall utilization rate by 50%, leading to cost savings in material procurement.
- 10% Reduction in Warehousing Costs: Optimized stock levels and better warehouse management led to a 10% reduction in overall warehousing costs, improving the company’s bottom line.
Conclusion
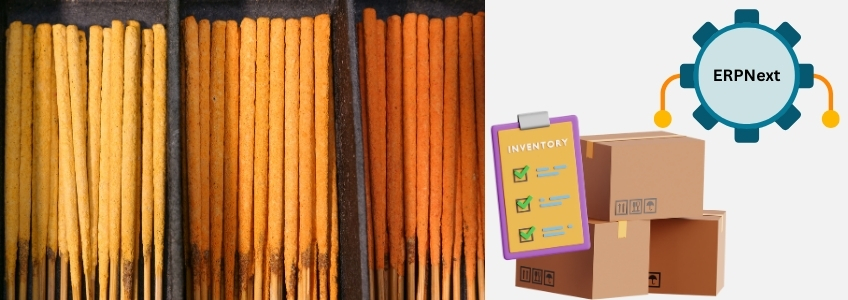
After associating with the ERPNext team at SKIL Global, Agarbathi Innovations got results that were significant and measurable. The company was able to tailor the solution to its unique requirements. This in turn led to a system that perfectly aligns with its business processes and drives significant improvements in efficiency and profitability. They reduced stockouts and improved inventory accuracy. They also saw faster order fulfillment and lower operational costs.
This success story here clearly demonstrates the power of ERPNext. It helps in streamlining inventory management for businesses of all sizes, particularly those with complex supply chains and multiple locations. ERPNext also serves as a valuable example for other businesses seeking to improve their inventory management processes and gain a competitive edge in the market.
If you are interested to achieve similar success stories, write to us!