Part 4 – Improvement Ideas to Sky-Rocket Productivity in a Factory
In the previous parts of this Lean case study, we’ve learned that our company had been tasked with identifying and solving a problem in 3 days within a limited budget. Within these circumstances, we were able to increase the company’s productivity by 150%!
In Part 1, we defined the problem and identified the goal statement. In Part 2, we elaborated on how we measured the current state – which is one of the most crucial steps in the successful implementation of Lean in any company. Finally, in Part 3, we covered how we pinpointed and analyzed the exact gaps in the factory’s operations. Here, we shall elucidate on the steps we took to overcome these gaps!
Summary of analysis
Here’s a quick recap of our findings from the analysis of the gaps in the factory’s operations:
- First, the slitting phase was performing optimally.
- Second, it was found that the stuffing phase was the bottleneck. This was because:
- Individuals worked to produce stuffed envelopes. Therefore, the flow was missing – which is the third Lean principle!
- Consequently, the inventory was haphazard.
- Lastly, the needed input was not placed near the actual point of use.
Improvement Ideas
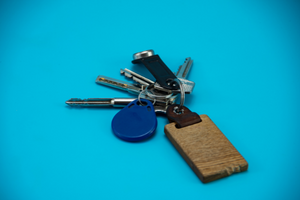
Based on a conversation with the factory’s contractor, we found that the average person stuffed 120 to 140 envelopes an hour. With certain improvement techniques, this number could be rocketed to 250+ enveloped per hour per person! Here’s what the ideas were:
New method
The goal of the improvement plan was simple – to produce at least 260 envelopes per person per hour. Consequently, this would help meet the turnaround time target. Taking into consideration that there were 9 people in the team, these are the calculations that we made:
- Total man-seconds needed to finish one envelope (based on a time study) = 10.9 seconds to tear, set and Z-fold, pick and count 50, stuff, paste, and verify.
- Man-seconds available per hour for 9 people = 9x60x60 = 32400 seconds.
- Needed output per hour = 32400/10.9 = 2964 envelopes
- Therefore, the expected output per person per hour = 2964/9 = 330 envelopes!
Hence, with this 100% efficiency, achieving 260 envelopes should not be a problem for the factory!
Proposed Cell Design to Run the Pilot
As a result of this new, proposed method which balanced manpower to flow and achieved the target per person per hour, the following layout was the most appropriate:
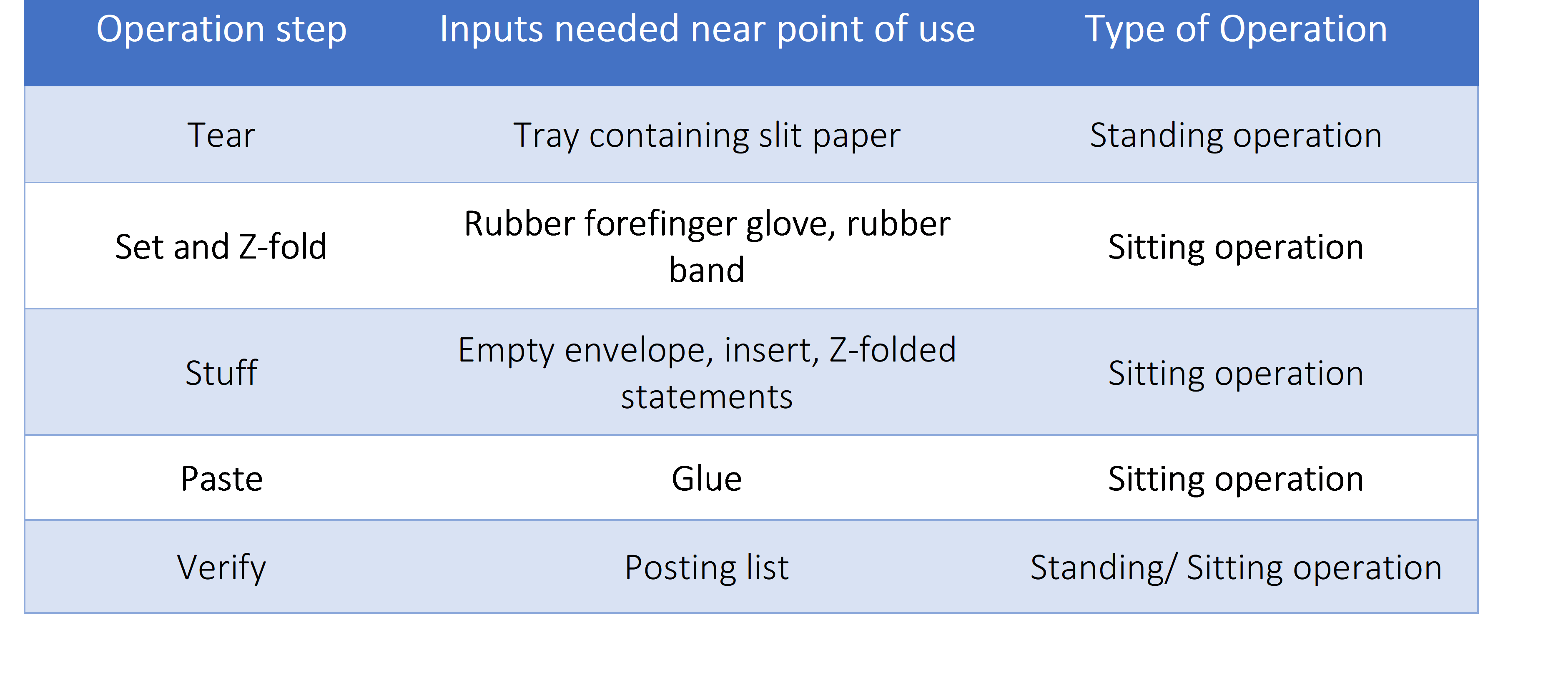
Table 1: Table of the required operation steps, and the corresponding inputs and position required
Therefore, the key is that the needed materials must be kept near the point of use within the cell design. To determine how close they should be and where they should be positioned, we adopted a 5S in Lean thinking approach. This helped us decide on a batch size of 50 envelopes to move from tear to verify, as doing a single piece took more time per envelope compared to doing an entire batch.
Now, keep in mind that at this stage, all of this was simply a conceptualization of the factory’s operations – a detailed and precise analysis. To test its efficiency, we had to carry out one of the most important final steps – i.e., the pilot run! In the next part, this is what we shall discuss.