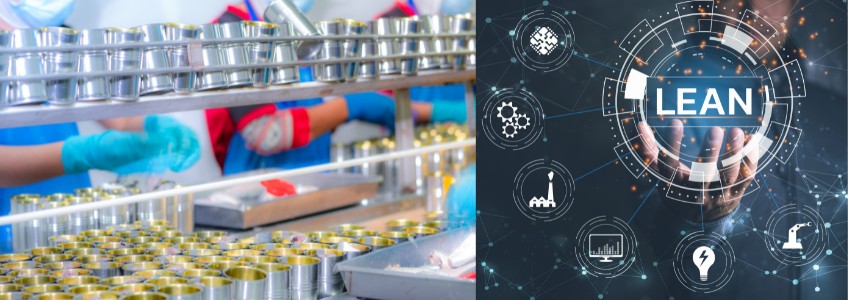
Introduction
The canned food manufacturing industry faces a unique set of challenges, especially when it comes to managing efficiency, product quality, and cost control. From fluctuating demand to maintaining high production standards, these challenges can make it difficult to keep operations running smoothly.
However, adopting Lean methodologies can significantly address many of these issues, leading to improved productivity and reduced waste. Additionally, equipping blue-collar workers with problem-solving skills is essential for sustainable improvements.
Key Challenges in Canned Food Manufacturing
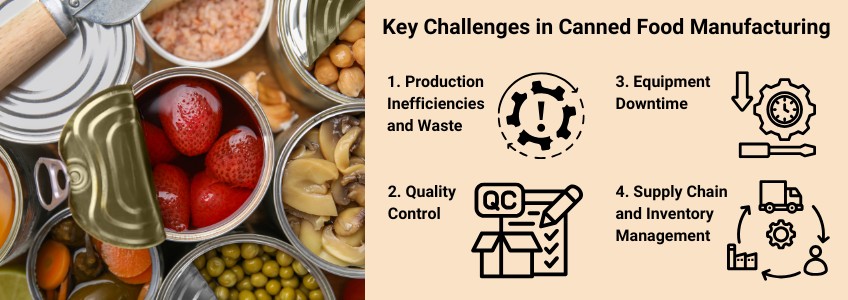
1. Production Inefficiencies and Waste
One of the most significant challenges in canned food production is inefficiency. The production process often involves multiple steps, including canning, sterilization, sealing, and labeling. Any inefficiency at any stage can lead to delays, higher costs, and wasted resources.
2. Quality Control
Maintaining consistent product quality is another challenge. Any deviation in temperature, processing time, or machinery calibration can lead to defects in the final product, affecting taste, texture, or shelf life.
3. Equipment Downtime
In any manufacturing environment, equipment downtime can be costly. Whether it’s maintenance issues or machine malfunctions, unplanned downtime can disrupt production schedules and result in lost profits.
4. Supply Chain and Inventory Management
Fluctuating demand and supply chain disruptions can create issues with raw material procurement and inventory management. Overproduction can lead to stockpiles of canned goods, while underproduction can cause supply shortages, leading to missed sales opportunities.
How Lean Methodologies Can Help
Lean methodologies focus on eliminating waste and improving process efficiency. In the context of canned food manufacturing, Lean can offer several benefits.
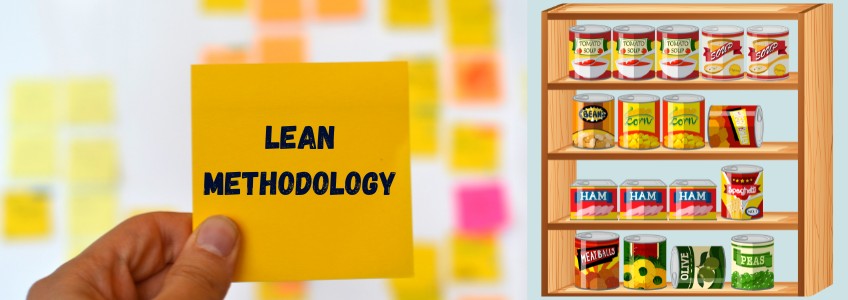
1. Reducing Waste and Improving Efficiency
By employing Lean tools like Value Stream Mapping (VSM), manufacturers can identify areas of waste in the production process. Whether it’s excess inventory, waiting time, or unnecessary motion, Lean allows companies to streamline processes, reduce waste, and increase throughput.
2. Enhancing Quality Control
Lean emphasizes continuous improvement, and through methods such as Root Cause Analysis (RCA), manufacturers can pinpoint the causes of defects and implement corrective actions. Techniques like Statistical Process Control (SPC) can be used to monitor production parameters and ensure consistency in product quality.
3. Predictive Maintenance and Minimizing Downtime
With Lean’s emphasis on standardizing work and predictive maintenance, manufacturers can proactively identify equipment issues before they lead to breakdowns. The introduction of Total Productive Maintenance (TPM) ensures that machines are always running at peak efficiency, minimizing downtime and improving production reliability.
4. Improving Supply Chain Management
Lean methodologies, such as Just-In-Time (JIT), can help align production schedules with customer demand, reducing overproduction and preventing stockpiling. This leads to a more responsive and flexible supply chain that reduces costs and improves cash flow.
The Importance of Problem-Solving Skills for Blue-Collar Workers
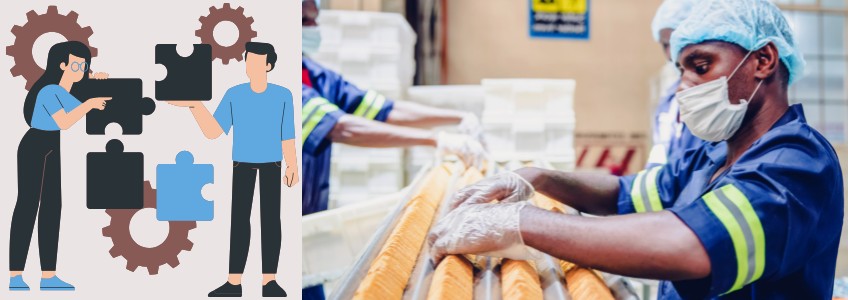
While Lean methodologies provide a framework for operational excellence, the successful implementation of these strategies relies heavily on the involvement of blue-collar workers. These workers are on the front lines of the manufacturing process, making them invaluable in identifying problems and proposing solutions.
By equipping blue-collar workers with problem-solving skills, manufacturers can create a culture of continuous improvement.
- Workers who understand Lean principles, such as Kaizen (continuous improvement), can identify inefficiencies in real-time and take immediate corrective actions.
- Additionally, fostering a problem-solving mindset among workers helps to improve communication, teamwork, and accountability on the factory floor.
- Offering training in problem-solving skills not only empowers employees but also improves overall productivity.
- Workers who feel confident in their ability to solve problems are more likely to suggest innovative solutions that drive operational improvements.
- This collaborative approach creates a more agile and responsive workforce, which is critical for success in the competitive canned food industry.
Conclusion
The canned food manufacturing industry faces several challenges that can impact both the quality and profitability of products. However, by implementing Lean methodologies, manufacturers can reduce waste, improve quality control, and increase efficiency. Furthermore, investing in problem-solving training for blue-collar workers is crucial to creating a culture of continuous improvement and ensuring the long-term success of Lean initiatives.
In the end, the key to overcoming challenges in canned food manufacturing lies in adopting a holistic approach. This approach should combine process optimization with skilled, empowered workers who are equipped to solve problems and drive positive change.
If you are interested to achieve similar success stories, write to us!