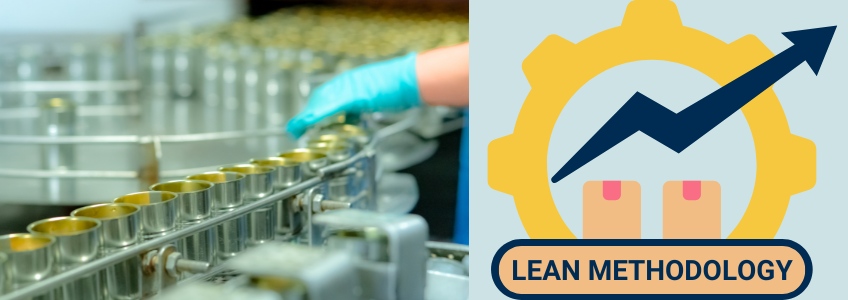
Introduction
The canned food manufacturing industry operates within a complex landscape of challenges. These include fluctuating demand, maintaining high production standards, controlling costs and ensuring product quality. All these hurdles can significantly impact operational efficiency and profitability.
This blog post will delve into the key challenges faced by this industry. It will also explore how the implementation of Lean methodologies, coupled with the empowerment of blue-collar workers, can drive significant improvements.
Key Challenges in Canned Food Manufacturing
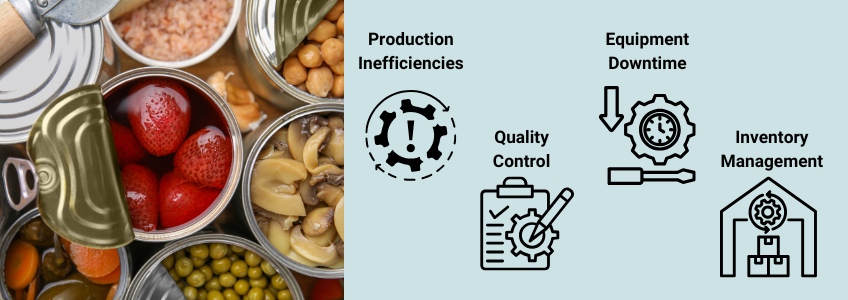
- Production Inefficiencies: Canned food production is a multi-step process. It includes canning, sterilization, sealing, and labelling. This in turn creates ample opportunities for inefficiencies. Delays, increased costs, and wasted resources can stem from inefficiencies at any stage.
- Quality Control: Maintaining consistent product quality is paramount. Variations in temperature, processing time, or machinery calibration can lead to defects that affect taste, texture, and shelf life.
- Equipment Downtime: Unplanned downtime due to maintenance issues or machine malfunctions can severely disrupt production schedules and result in substantial financial losses.
- Inventory Management: Fluctuating demand and supply chain disruptions can create challenges in raw material procurement and inventory management. Overproduction leads to stockpiling, while underproduction can cause supply shortages, impacting sales.
The Power of Lean Methodologies
Lean methodologies, with their focus on eliminating waste and streamlining processes, offer a powerful solution to these challenges.
- Reducing Waste and Improving Efficiency: Through tools like Value Stream Mapping (VSM), manufacturers can identify and eliminate waste, such as excess inventory, waiting time, and unnecessary motion, leading to increased throughput and reduced costs.
- Enhancing Quality Control: Lean principles, such as Root Cause Analysis (RCA) and Statistical Process Control (SPC), enable manufacturers to identify the root causes of defects and implement corrective actions to ensure consistent product quality.
- Predictive Maintenance and Minimizing Downtime: Lean emphasizes standardized work and predictive maintenance, enabling proactive identification and resolution of equipment issues before they lead to costly downtime. Total Productive Maintenance (TPM) further ensures optimal machine efficiency.
- Improving Supply Chain Management: Just-In-Time (JIT) principles can align production schedules with customer demand, minimizing overproduction and preventing stockpiling. This leads to a more responsive and flexible supply chain, reducing costs and improving cash flow.
Empowering Blue-Collar Workers for Sustainable Improvement
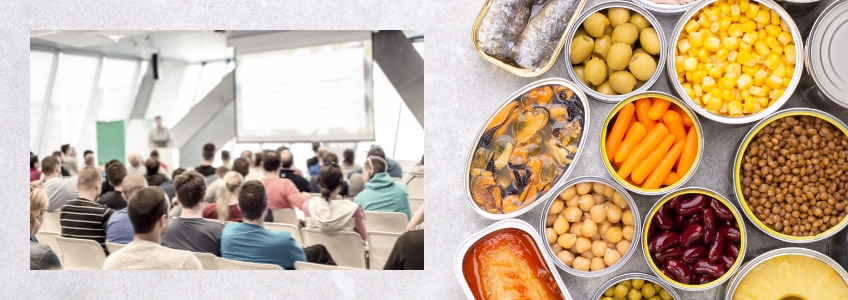
The successful implementation of Lean principles heavily relies on the active involvement of blue-collar workers. As frontline employees, they possess invaluable insights into the production process and can play a crucial role in identifying and solving problems.
Equipping blue-collar workers with problem-solving skills through training programs like Kaizen (continuous improvement) empowers them to identify inefficiencies in real-time. Thereafter, these workers can also take corrective actions. This fosters a culture of continuous improvement, enhances communication, and improves teamwork and accountability on the factory floor.
Empowered workers are more likely to contribute innovative solutions that drive significant operational improvements. This collaborative approach creates a more agile and responsive workforce, a critical factor for success in the competitive canned food industry.
Conclusion
Hence, by embracing Lean methodologies and empowering their workforce, canned food manufacturers can effectively address the challenges they face. This approach not only enhances efficiency and reduces waste but also improves product quality, minimizes downtime, and strengthens supply chain management.
Lean methodologies offer a holistic approach that combines process optimization with a skilled and empowered workforce. Such a practice is the key to achieving sustainable success in the dynamic canned food manufacturing industry.
If you are interested to achieve similar success stories, write to us!