Operational Excellence:
The success story of an apparel manufacturing company
Operational excellence and Lean are the key elements to organizational success. Therefore, our goal is to help companies incorporate these elements into the depths of an organization’s culture. In this case study, we’ll trace our journey in instilling operational excellence to elevate the functioning and operations of an apparel manufacturing company. Their main aim was to facilitate an all-around improvement because their factory was incurring losses. Here’s how we went about it:
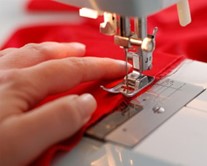
Challenges to Operational Excellence
While surveying and observing the operations over time, these are the challenges that we noted the apparel manufacturing company was facing:
- First, the order quantities per style were small.
- Second, there were short shipments.
- Third, there were air shipments.
- Fourth, the customer claims were a challenge.
- Fifth, the actual efficiency was less than the budgeted efficiency % for the styles.
- Next, it was taking a long time to reach the peak efficiency %.
- Lastly, there was a long changeover time from one style to another.
Solutions to the Operational Excellence Issues
These were the solutions that we came up with to solve their OpEx problems:

- First, we had to build a strong base, comprising of 5S, Visual Factory, Autonomous Maintenance.
- Next, we proposed current state value stream mapping.
- Third, we carried out a future state design and guided the identification and prioritization of Kaizens. These included:
- Learning classes (in local language) for all supervisors, production managers, assistant production managers, floor in-charge, and sectional heads. The syllabus and study material were designed for everyone’s work area.
- Gemba and Kaizen programs were conducted every month to help in its application.
- Daily (Line meetings), weekly (Factory meetings), and monthly (Management meetings) performance reviews we carried out, followed by corrective and preventive actions.
- Lastly, a Lean Manufacturing System was implemented. This included an order execution approach for ‘Pull Production’ via Quick Changeover, Line Balance, Throughput Flow and Kanban techniques.
Apart from these, another crucial key to ensuring the apparel manufacturing company’s success was Top Management Commitment on a long-term (3 years) basis.
Results of OpEx in the Apparel Manufacturing Company
Here’s a look at a graphical representation of the results of the successful implementation of operational excellence in the company:
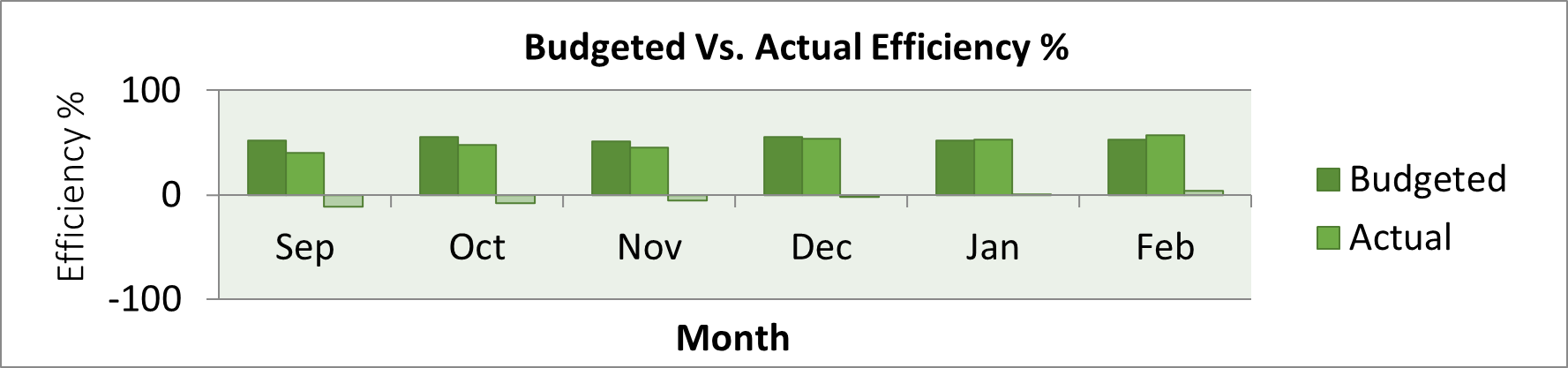
Remember that these are just some of the possible benefits of integrating operational excellence into your company’s framework! By combining the power of technology, science, and people engagement, we ensure an enjoyable and exciting improvement journey! One’s own success story is the best form of motivation to continue this journey, so check out other case studies where we implemented OpEx to guarantee organizational success!