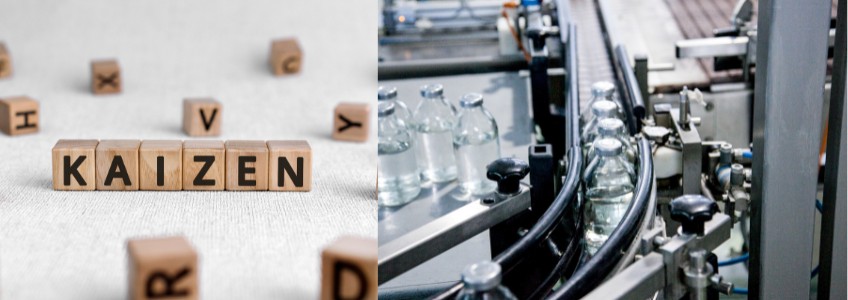
Introduction
In the pharmaceutical industry, where precision, compliance, and efficiency are paramount, achieving operational excellence is a constant challenge. With rising regulatory demands and competitive pressures, companies need strategies that not only optimize processes but also foster a culture of continuous improvement. One such strategy is Kaizen.
Kaizen is a Japanese philosophy meaning “good change” or “continuous improvement.” It emphasizes small, incremental changes that collectively lead to significant improvements over time.
In this blog, we’ll explore how Kaizen principles can transform pharmaceutical operations by reducing waste, enhancing quality, and ensuring compliance—all while empowering employees to drive meaningful change.
What is Kaizen in Pharma, and Why Does it Matter?
Kaizen is a systematic approach to improving processes through small, ongoing positive changes rather than large-scale transformations. In the pharmaceutical sector, it aligns perfectly with the industry’s goals of maintaining high-quality standards and adhering to stringent regulatory requirements.
Why is Kaizen important for pharma?
- It ensures compliance with Good Manufacturing Practices (GMP).
- It reduces waste and inefficiencies in manufacturing processes.
- It improves product quality and consistency.
- It fosters employee engagement and innovation.
Pharmaceutical companies can create a culture of continuous improvement, that drives both efficiency and sustainability, by embedding Kaizen into daily operations.
How to Implement Kaizen in Pharma
1. Foster a Culture of Continuous Improvement
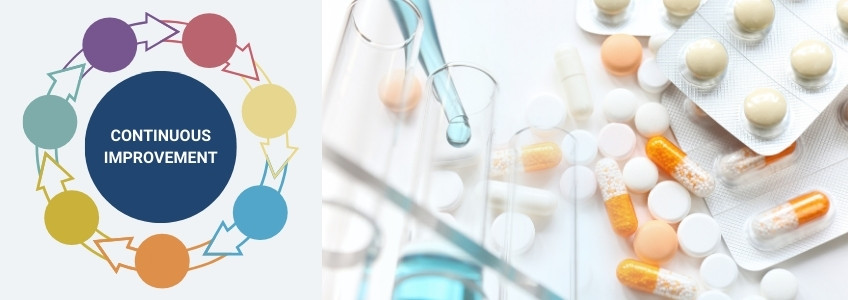
Kaizen starts with mindset. Encourage employees at all levels to identify inefficiencies and suggest improvements. This bottom-up approach not only empowers staff but also ensures that changes are practical and impactful.
Steps:
- Conduct regular Gemba walks (on-site observations) to identify bottlenecks.
- Create suggestion systems where employees can propose ideas for improvement.
- Recognize and reward contributions to foster motivation.
2. Standardize Processes
Standardization is key to maintaining quality and compliance in pharma manufacturing. The SDCA (Standardize, Do, Check, Act) cycle helps establish consistent procedures that reduce deviations and errors.
Steps:
- Document Standard Operating Procedures (SOPs) for all critical tasks.
- Train employees on these SOPs to ensure adherence.
- Regularly review and update SOPs based on feedback and improvements.
3. Use the PDSA Cycle for Continuous Improvement
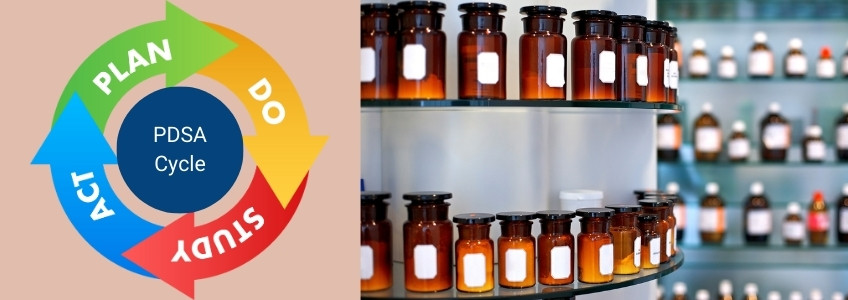
Once processes are standardized, the PDSA (Plan, Do, Study, Act) cycle comes into play. This iterative approach identifies areas for improvement and implements changes systematically.
Steps:
- Plan: Identify specific areas for improvement (e.g., reducing batch cycle times).
- Do: Implement small-scale changes as pilots.
- Study: Analyze the results of these changes using metrics like efficiency or defect rates.
- Act: Scale successful improvements across the organization.
4. Reduce Waste
Waste elimination is a cornerstone of Kaizen. In pharma, waste can take many forms—time delays, material wastage, or inefficient workflows.
Steps:
- Map out value streams to identify non-value-added activities.
- Optimize workflows by eliminating redundant steps.
- Invest in automation tools to reduce manual errors.
5. Empower Employees
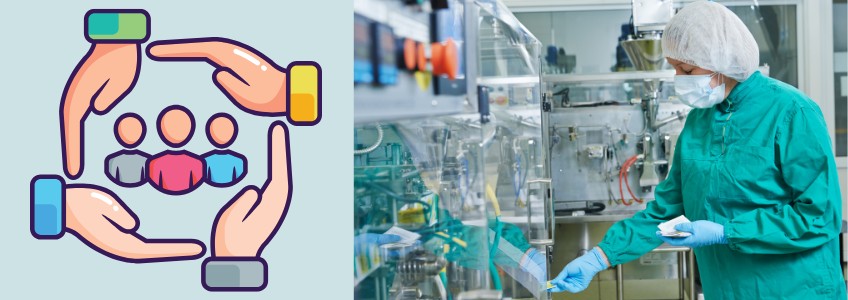
Employee involvement is critical for Kaizen’s success. By giving workers ownership of their tasks and involving them in decision-making processes, companies can unlock innovative solutions.
Steps:
- Organize cross-functional teams for brainstorming sessions.
- Provide training programs to enhance problem-solving skills.
- Create transparent systems to track progress and share results with employees.
6. Measure Progress
To sustain improvements, it’s essential to track performance metrics regularly. Transparency in reporting builds trust and encourages further participation.
Steps:
- Use Key Performance Indicators (KPIs) like cycle time reduction or defect rates.
- Share progress reports across teams to highlight successes.
- Continuously refine metrics based on organizational goals.
Tips for Success with Kaizen in Pharma
- Start small: Focus on one process or department before scaling up.
- Be patient: Kaizen is about gradual change; results may take time but are sustainable.
- Ensure compliance: Always align improvements with GMP guidelines to avoid regulatory risks.
- Promote collaboration: Encourage teamwork across departments for holistic improvements.
- Celebrate wins: Recognize achievements to maintain momentum and employee engagement.
Conclusion
Kaizen proves that small changes can lead to big impacts in the pharmaceutical industry. By fostering a culture of continuous improvement, standardizing processes, reducing waste, and empowering employees, pharma companies can achieve operational excellence while maintaining compliance and delivering high-quality products.
Ready to implement Kaizen in your operations? Write to us today.