Case Study on Applying Lean Principles in a Newspaper Company: Part 4
This is the fourth and last part of our case study, which focuses on a newspaper company we worked with to solve their problem of delivering newspapers on time. In the first part of our case study, we covered the observations that we made during the 4-step newspaper-printing process. In the second part, we elaborated on the process of mapping the current state value stream. Then, in the third part, we went over the solutions we arrived at to tackle the bottlenecks of various steps in the process. In this part of the case study, we will highlight how we planned out the future state and tested kaizens!
Testing Kaizens
The best way to carry out Kaizens is to carry them out!
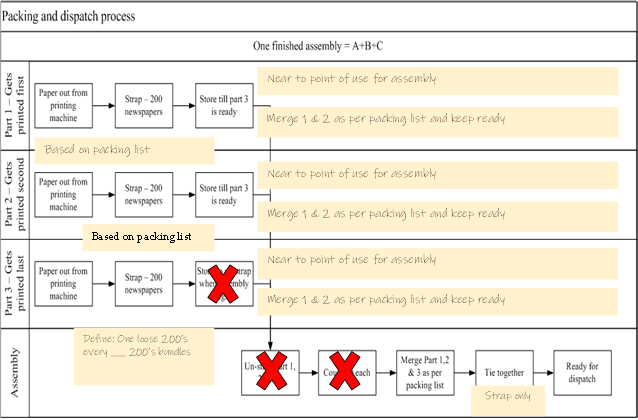
Figure 1: Preparation for implementing Kaizens
Especially in the case of Kaizens, it’s important to test out ideas to ensure their workability. Implement your ideas with a sense of urgency – so if you fail, fail fast! While failure isn’t a loss, the excess time taken to fail sure is.
Ideal State
The first step in establishing an ideal state is to identify the bottleneck. In this case study, we identified packaging to be the bottleneck. What could be the ideal state? No packaging! So, ideally, the newspaper printing machine would print and then automatically pack newspapers as per the packing list.
- Ideal state (Theorized):
- First, parts 1, 2, and 3 are printed simultaneously using three separate lines.
- Second, auto-collate newspapers according to packing list and strap.
- Third, auto-pack.
- Fourth, store them around dispatch – last in and first out.
- Lastly, use a conveyor belt to load the trucks.
- Future state: Carry out this future state within two weeks of discovery.
- ‘Flow’ packing using Lean thinking ideas to ensure, on-time delivery from tomorrow!
- We decided to carry out an ‘assembly cell’ to achieve flow and balance in packing. To design this, we carried out the following calculations:
- Demand: 30600 parcels in 150 min
- TAKT time = 17.67 sec (0.29 min)
- Include the cell operations
- Count Part 3 according to packing list:
- Average copies a parcel = 50
- Time (seconds) to count a copy = 0.25 seconds
- Total counting time a parcel = 0.25*50 = 13 seconds
- Total parcels capacity a minute = 5 to 6, from counting perspective
- Number of counting operators = 17.6/13=1.35 (say 2 people)
- Strap the parcel quantities and store them in predefined area to load into the truck:
- Average time to strap a bundle of 200 = 11s / bundle of 200
- Number of strapping operators = 17.6/11 = 1.6 (with 2 people).
Therefore, to execute the future state, we decided to eliminate the steps with ‘X’ mark in the above diagram.
Aligning to Demand
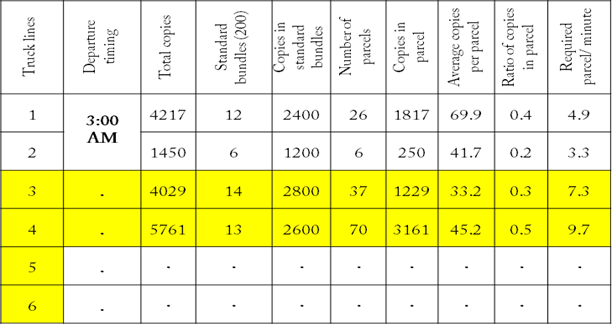
Figure 2: Align workflow to the demand
When meeting demands, let’s consider the first row in the picture above. Truck lines 1 and 2 should leave the factory at 3:00 am. The total number of copies sent in each of these trucks is 4217 and 1450 respectively, and each of these standard bundles was 12 and 6 respectively, as per the packing instructions.
If 200 pieces make one standard bundle, a total of 2400 and 1200 copies should be packed as a standard bundle for the two row items. As per the packing list, the number of parcels (i.e., a loose quantity not amounting to 200) was 26 and 6 respectively, and the total number of copies in these two parcel quantities are 1817 and 250. Therefore, the average number of copies per parcel was 69.9 and 41.7, which was derived from the total number of parcels and parcel quantity. Furthermore, the ratio of copies in parcel to the total copies was found to be 0.4 and 0.2 for the first two row items in the packing list.
To understand the demand and work planning, ‘parcels load levelling’ was aligned with ‘Heijunka’ in Lean. Therefore, two points were clear:
- Make parcels right from the beginning of the flow. Level the parcel making load across the working time (start to end of the work).
- Feed the parcel making ‘cell’ according to the ratio of copies in parcel for example a ratio of 0.5 (ratio of copies in parcel) means one every two 200’s printed should go to parcel making cell.
Designing the cell for packing
Assembly line design for Packing:
- Number of operators in the cell = 4.
- Number of people who make parcels = 2
- Number of people who strap standard bundles with parcel (loose quantities) = 2
- 1 in 3 standard bundles (200 newspapers) should go to parcel making cell.
- 1 in 3 classified bundles (200 newspapers) should go to parcel making cell.
- Keep the packing slip on the table, in front of ‘parcel makers’.
- Zero inventory between – ‘making parcel’ and ‘strapping’ (Flow)
- Locate a place for everything. (5S)
- Keep extra strapping rolls next to the machines. (Changeover)
- Eliminate counting 50’s (Over-processing waste)
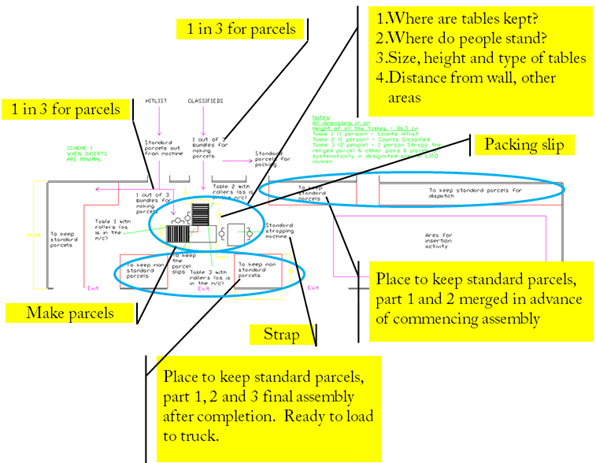
Figure 3: Design of the layout (based on cellular flow principles)
For our pilot, we conducted 2 trials. I ran one myself and supervised the other. The following results were achieved:
- First, every truck left before time.
- Second, the assembly cell was successful!
The success of the pilot created an environment of excitement and motivation in the company! Though this is still the intermediate future state, and the ideal state has yet to be attained, it is a start!
Here are the detailed results of both trials in the pilot:
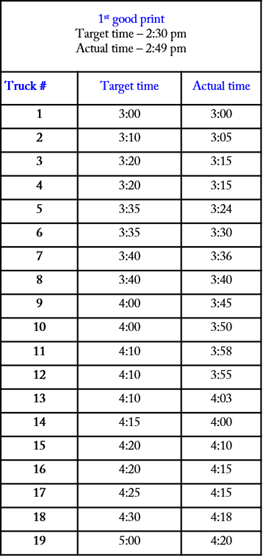
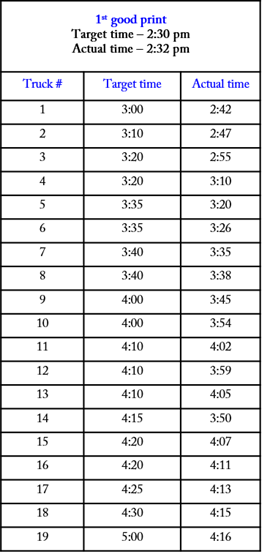
The ideas worked in both trials of the pilot, and the trucks left earlier than their scheduled time.
Summing it up with A3
Here’s the complete story of our work at the newspaper company, in an A3 format:
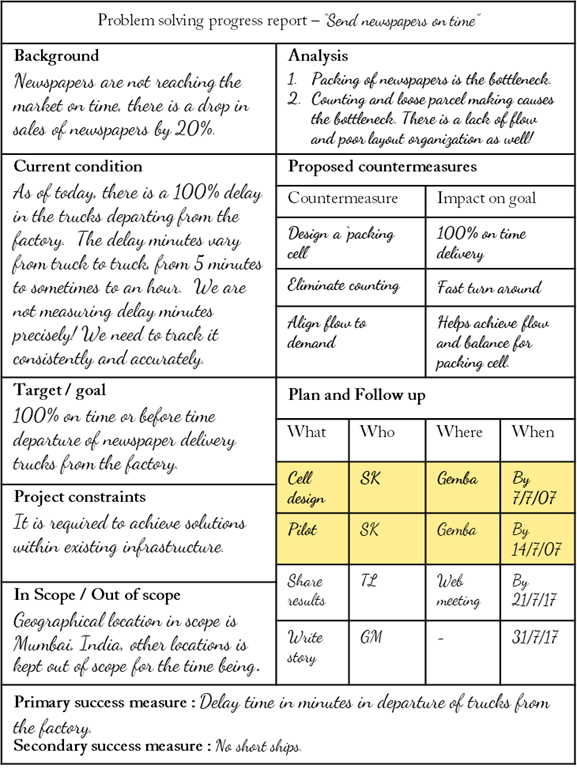
Figure 4: Success story captured in A3 format