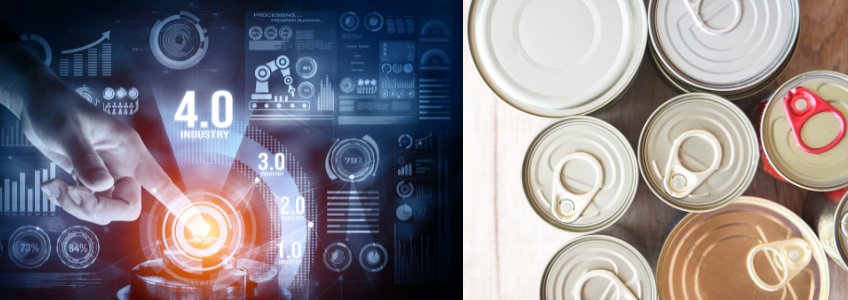
Introduction
The canned food industry represents about 10% of global food production, making it one of the most significant sectors in food processing.
With rising consumer demand for high-quality, safe, and efficient food products, the industry faces mounting pressure to increase productivity and improve quality. This is driving the adoption of new strategies and technologies. As a result, we see the rise of Canned Food 4.0.
Canned Food 4.0 refers to the integration of advanced technologies like automation, robotics, artificial intelligence (AI), and the Internet of Things (IoT) into canned food production processes. These technologies are transforming how the industry operates by improving operational efficiency and ensuring product quality.
In this post, we’ll explore the key components of Canned Food 4.0, its benefits, and how it contributes to operational excellence in the modern manufacturing landscape.
What is Canned Food 4.0 and Why Does It Matter?
Canned Food 4.0 describes the digital and technological transformation of the canned food industry. Through the use of automation, AI, IoT, and robotics, manufacturers are revolutionizing their operations to improve product quality, enhance efficiency, and reduce costs.
This matters because, in a highly competitive market, food manufacturers must find innovative ways to reduce downtime, minimize waste, and meet evolving consumer expectations.
By embracing Canned Food 4.0, manufacturers can create more resilient, efficient, and responsive production systems, ensuring that they remain competitive while complying with increasingly stringent food safety standards.
How to Implement Canned Food 4.0 for Operational Excellence
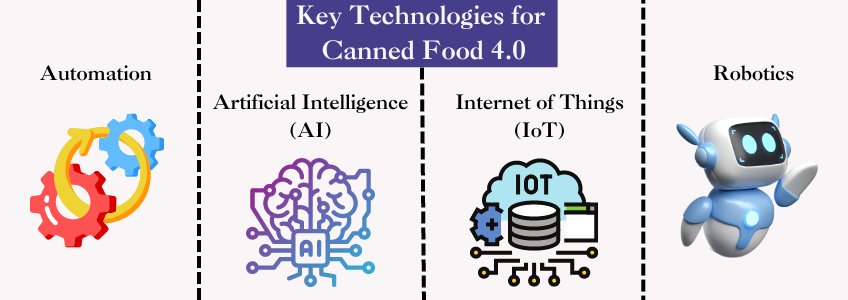
1. Automation: The Backbone of Efficiency
Automation, the cornerstone of Canned Food 4.0, involves deploying machines to execute repetitive tasks like filling, sealing, and labeling cans. This technology not only increases production speed but also enhances accuracy and consistency, reducing the margin of error in product quality.
Automated systems can handle vast volumes of production, helping manufacturers achieve greater operational efficiency while freeing up human workers for more complex tasks.
For example, some of the largest global food companies have automated up to 70% of their production lines, achieving a 30% increase in overall efficiency and reducing production time by 25%.
2. Artificial Intelligence (AI): Data-Driven Optimization
AI-powered systems enable manufacturers to optimize production by analyzing real-time data, predicting equipment failures, and identifying inefficiencies in the process.
AI algorithms can be used to monitor production quality, analyze historical data, and suggest improvements to minimize downtime and improve productivity.
By implementing AI-powered quality control, companies have been able to reduce product defects by up to 15%, leading to improved customer satisfaction and significant cost savings.
3. Internet of Things (IoT): Real-Time Monitoring and Traceability
IoT facilitates communication between machines and devices, allowing manufacturers to collect and share data across their production lines.
Sensors embedded in equipment monitor conditions like temperature, humidity, and pressure, providing real-time insights into production processes. This helps manufacturers maintain optimal conditions and ensures that food safety standards are met.
A major food company that implemented IoT across its production line saw a 25% reduction in energy consumption and a 20% improvement in traceability, leading to faster and more accurate product recalls when necessary
4. Robotics: Precision and Safety
Robots are being used to perform tasks that are either too dangerous or intricate for human workers. This includes handling hot materials, working in hazardous environments, and executing high-precision tasks such as packaging and sorting.
The precision of robotics ensures uniformity in production and reduces the risk of workplace accidents.
In some factories, robotic systems have reduced workplace injuries by 40% while also increasing throughput by as much as 20%.
The Benefits of Canned Food 4.0
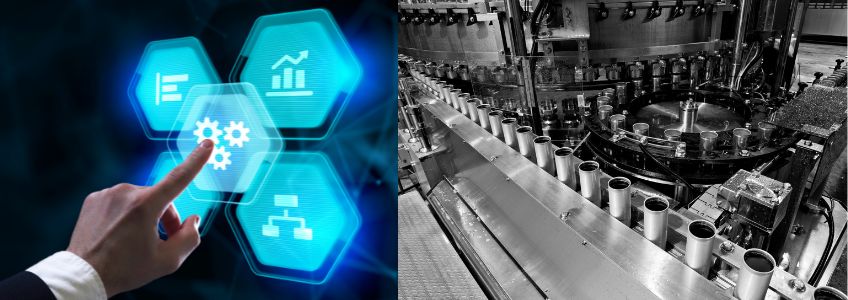
1. Increased Efficiency and Productivity
Automation and robotics significantly reduce labor costs, improve production speed, and optimize workflow. AI and IoT technologies provide real-time insights that enable manufacturers to identify bottlenecks and inefficiencies quickly.
These technologies help companies achieve up to a 40% increase in production capacity.
2. Enhanced Product Quality
Automated systems ensure consistent quality across production lines by reducing the risk of human error.
AI-powered quality control systems detect defects earlier in the production process, reducing waste and improving overall product reliability. Some companies have reported a 20% improvement in product consistency through automation.
3. Improved Traceability and Compliance
IoT technologies provide end-to-end visibility in the supply chain, ensuring that products are traceable from production to delivery.
This capability helps manufacturers comply with food safety regulations and execute product recalls more effectively. With enhanced traceability, companies have reported a 30% reduction in food safety incidents.
4. Greater Flexibility and Agility
Robotics and automated systems are designed to adapt quickly to changing consumer preferences or market demands. This flexibility allows manufacturers to introduce new products or modify existing processes without major disruptions.
As a result, companies can respond faster to market shifts, improving their competitive edge.
5. Cost Reduction
By optimizing production efficiency, reducing energy consumption, and minimizing waste, Canned Food 4.0 helps manufacturers lower their operating costs.
Companies adopting these technologies have seen up to a 20% reduction in overall operational expenses.
Tips for Implementing Canned Food 4.0
- Prioritize Key Areas: Start with automating core processes that will have the most significant impact on efficiency and quality. Identify areas where robotics and AI can enhance precision and output.
- Train Your Workforce: Invest in training to help employees understand how to work alongside advanced technologies like AI and IoT. A skilled workforce ensures seamless integration of these systems.
- Utilize Data for Continuous Improvement: Leverage the data collected from IoT devices and AI analytics to continuously monitor and refine your processes, ensuring long-term operational excellence
Conclusion: The Future of Canned Food 4.0
The food processing industry is at a turning point, and the shift toward automation, AI, IoT, and robotics is becoming more critical for long-term success.
Over the next decade, the use of automation in the canned food industry is expected to grow by 5% annually, driven by the need for greater efficiency, higher product quality, and improved sustainability.
Canned Food 4.0 is not just a trend; it is the future of the food industry. Companies that invest in these technologies today will be positioned for greater success tomorrow, as operational excellence becomes the key to thriving in an increasingly competitive global market.
If you are interested to achieve similar success stories, write to us!