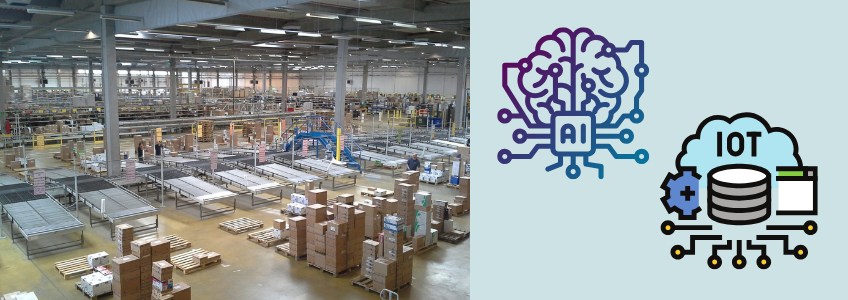
“The best way to predict the future is to create it.” – Peter Drucker
Introduction
In the dynamic world of warehousing, the above-mentioned quote by Peter Drucker rings truer than ever. Imagine a warehouse where every piece of machinery knows when it’s about to fail. A warehouse where shelves “speak” to forklifts, guiding them precisely where to go. This isn’t science fiction—it’s the reality of 2025, where Artificial Intelligence (AI) and the Internet of Things (IoT) are revolutionizing how we store, move, and manage goods.
In 2025, AI and IoT integration are no longer optional but essential for warehouses to remain competitive in a rapidly evolving market. This blog explores the latest trends in warehousing and takes a deep dive into one standout trend: predictive maintenance powered by AI and IoT.
The Transformation Begins
A few years ago, warehouses were struggling with age-old issues: downtime, inaccurate inventory, and unpredictable equipment failures. Fast forward to today, and the game has changed.
With AI and IoT as the architects of this transformation, warehouses have become smart ecosystems—efficient, predictive, and highly responsive. These innovations aren’t just tools; they’re teammates that make decisions, solve problems, and ensure smooth operations.
Key Warehouse Trends in 2025
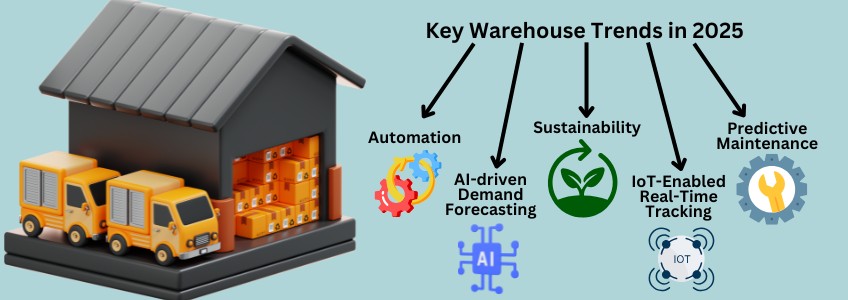
To fully appreciate the shift, let’s step into a modern warehouse and see what’s happening:
- Automation is Everywhere: Autonomous Mobile Robots (AMRs) zip through aisles, collecting items faster than a human ever could. Automated Guided Vehicles (AGVs) replace manual carts, reducing errors and saving time.
- AI-Driven Demand Forecasting: Gone are the days of guessing. AI crunches historical data and market trends to predict exactly what customers want and when. Overstocking? A thing of the past.
- Sustainability is No Longer Optional: Solar panels, energy-efficient cooling systems, and eco-friendly packaging are now standard. Warehouses are as green as they are smart.
- IoT-Enabled Real-Time Tracking: Picture this: a warehouse manager opens an app and sees every product, every machine, and every asset in real time. IoT sensors make this possible.
- Predictive Maintenance: This is the crown jewel. With AI and IoT working hand-in-hand, warehouses don’t wait for equipment to break. They know when it will break and fix it beforehand.
Predictive Maintenance: The Unsung Hero
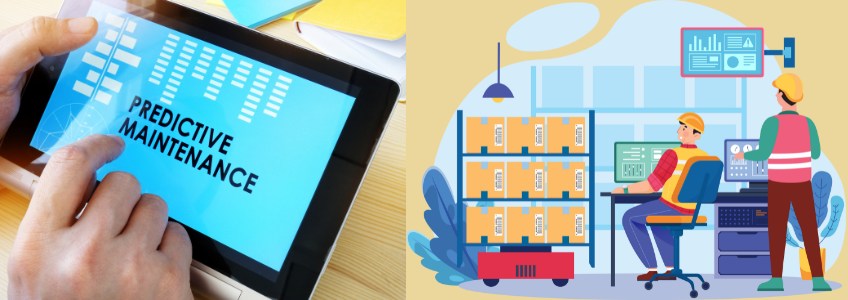
Let’s focus on predictive maintenance—a silent revolution saving businesses millions while keeping operations smooth.
A Day in the Life of Predictive Maintenance
Imagine a conveyor belt in a bustling warehouse. It hums along, moving packages efficiently. But suddenly, IoT sensors detect unusual vibrations. The system flags this as a potential problem and alerts the maintenance team.
Before the belt can break, technicians replace a worn-out component. The downtime? Just 10 minutes. The cost? Minimal. The alternative? Hours of disruption and thousands of dollars in lost productivity
Here’s how predictive maintenance works its magic:
- IoT Sensors Collect Data: These tiny devices monitor every vital sign of equipment—temperature, pressure, vibration, and more.
- AI Analyzes Patterns: AI algorithms process this data to find anomalies and predict when something might go wrong.
- Proactive Alerts: Maintenance teams receive alerts before issues become problems. Repairs are planned, not rushed.
Assets Monitored by IoT
From the smallest component to the largest system, IoT ensures no detail is overlooked:
- Conveyor Systems: Monitor motor health, belt alignment, and speed.
- Refrigeration Units: Keep temperature-sensitive goods safe with real-time alerts.
- Forklifts and Material Handlers: Track usage and prevent overworking critical equipment.
- Power Systems: Ensure consistent energy for uninterrupted operations.
- Fire Safety Systems: Provide instant warnings if conditions become hazardous.
Real-Life Stories: How Giants Lead the Way
Amazon: Leading by Example
Amazon’s warehouses are legends in their own right. But what keeps them running during Black Friday chaos? Predictive maintenance. IoT sensors and AI systems ensure conveyor belts and robotic arms work flawlessly. This proactive approach has slashed downtime by 30%, delivering packages faster and cheaper.
Walmart: Refrigeration Revolution
Walmart employs IoT to monitor thousands of refrigerated units globally. When a sensor detects a temperature anomaly, the system springs into action. Spoilage has dropped by 20%, saving millions annually.
Siemens: Smarter Every Day
At Siemens, predictive maintenance isn’t just a tool—it’s a strategy. IoT sensors on robotic arms detect wear before it becomes a problem. Result? Maintenance costs are down 25%, and high-demand periods are smoother than ever.
Why This Matters
The beauty of predictive maintenance lies not just in efficiency but in storytelling. Every sensor tells a story—of a conveyor belt working hard, of a refrigeration unit battling the heat, of a forklift carrying its weight. These stories are the backbone of smarter warehouses.
As AI gets better, the future promises even more. Think of self-healing systems where machinery doesn’t just detect problems—it fixes them.
Conclusion
The warehouse of 2025 is a marvel of technology and foresight. With AI and IoT driving predictive maintenance, businesses are unlocking new levels of efficiency, safety, and cost savings.
For warehouses still clinging to outdated methods, the message is clear: the future waits for no one. It’s time to embrace these innovations, or risk being left behind.
Therefore, for warehouses that are looking to future-proof their operations, embracing predictive maintenance is not just an option—it’s a necessity.
If you are interested to achieve similar success stories, write to us!