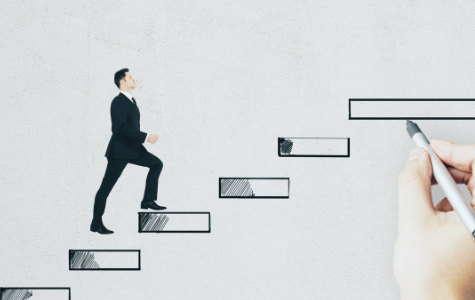
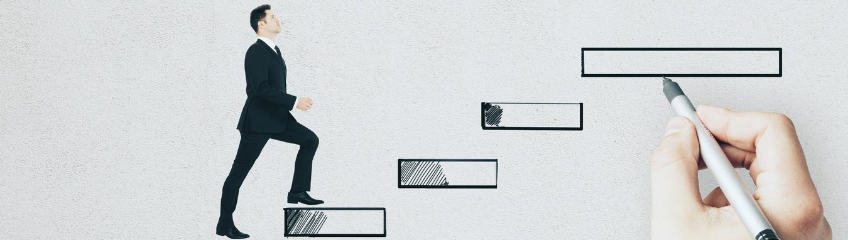
A Guide to Value Stream Mapping- Part 3
Two of the most crucial tools to organizational success are value stream mapping and long-term planning. They are a part of the major umbrella of Lean thinking, which includes 5 principles – namely, value, value stream, flow, pull, and perfection. In this series of articles, we provide you with a guide to map a value stream optimally, through a case study.
In the first and second parts of this case study, we have covered the importance of value stream mapping, and its first principle – i.e., to define ‘value’. Here, we will find out about the execution and importance of the following principles.
Second Principle: Map the “Value Stream”
The value stream map deals with one of the most important keys – i.e., to unearth what we don’t know. There are two types of value stream maps:
- First, there is the Current State Value Stream Map (CSVSM), which captures the ‘as-is’ state of a process.
- Second, there is the Future State Value Stream Map (FSVSM), which presents the ‘should-be’ state of a process once the non-value-added time is eliminated.
To develop FSVSM, a basic working knowledge of Lean tools is a necessity, which includes:
- Kanban
- Single piece flow
- Visual factory ideas
- Cellular manufacturing
- FIFO (First in, first out)
- 5S
- TAKT time, Line balancing and flow ideas
- JIT (Just in time) production
- Andon
- Poka Yoke
- Load Levelling
- Autonomation
- TPM (Total Productive Maintenance)
- Technology upgrade
- Automation
How to Organize for Value Stream Mapping?
Mapping the value stream process requires a degree of organization and planning to go into first. This is how you can organize the value stream mapping process:
- First, define the starting and ending point of the process in scope. Some examples of this include ‘receiving a customer order to shipping it to the customer’, ‘receiving material-need indent to issuing the raw material to the indenter’, and ‘incoming calls from customers to call resolved’, etc.
- Second, identify the impacted people who should take part in the mapping. This includes the people who identify with the process map in scope.
- Third, prepare a plan to begin and complete the CSVSM. For instance, the plan may look like this:
1. Meet on 22/12 and make a process map. Following this, identify the content of the data box and plan for data collection. The table below highlights these contents. However, remember that ‘what data is needed’ depends entirely on what the goal is.
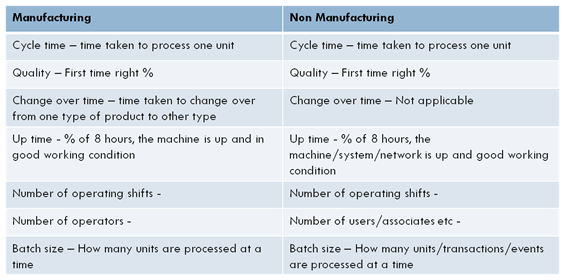
2. Collect the data from 23/12 to 28/12.
3. Populate the collected data on your CSVSM on 29/12.
- Fourth, make a rough process map, which will incorporate the series of steps between the start and endpoints. Each step of the process map can be a ‘box’ in the value stream flow. Furthermore, you can combine the steps as per your judgment and experience of the process.
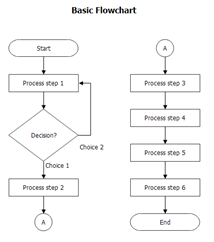
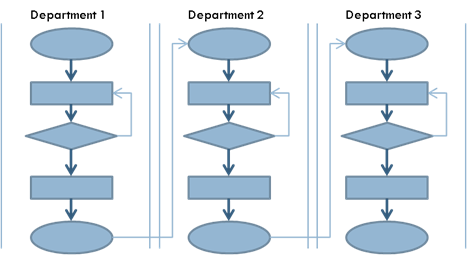
- Lastly, convert the process map to a ‘value stream map’. While doing so, the best method is to follow the process for one unit of production as it happens. Don’t push it – rather, allow it to take place the way it normally does. The least preferred method is to interview the impacted people, the doers, and then draft it.
Use the following steps to create a value stream map:
- Step 1 – Understand the customer
- Step 2 – Map the production flow.
- Step 3 – Map the material flow.
- Step 4 – Map the information flow.
- Step 5 – Find the Value-Added Ratio.
- Step 6 – Identify ideas to create flow and pull.
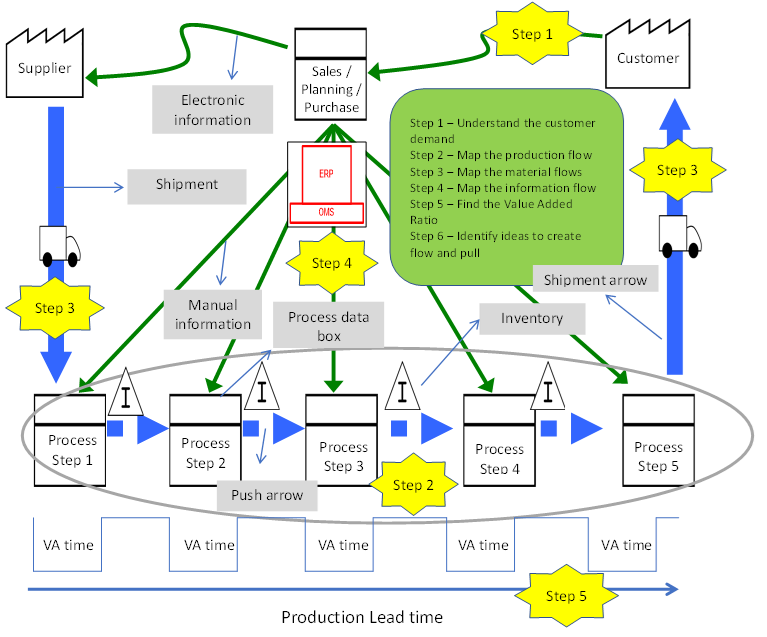
For those who are placed in non-manufacturing roles, the material flow may disappear while the information flow remains. Once the value stream map is complete as per the needed levels of adequacy and accuracy, find the value-added ratio:
Value added ratio (%) = (total VA time)/ (total time to complete the customer order) x 100.
Based on my experience in this industry, the material undergoes value addition in less than 5% of the time. On the other hand, the material is likely to wait for one reason or the other during the remaining 95% of the time.
Challenges faced during Current Value Stream Mapping:
- First, confusion regarding classification of value-added and non-value-added activities.
- Second, there is usually no time and participants tend to remain busy.
- Third, there may be issues with data, including not being captured, inconsistent capture. Reasons for this could range from not having time to having a scarcity of resources.
- Next, there may be a fear of the unknown. Therefore, this could generate resistance.
- Lack of ownership of the data and people doubting the data may be among the several additional reasons that pose challenges to CSVSM. Most often, this happens when data suggests notable gaps and issues.
- Fifth, a major challenge is the constant adjustments that are made to the data to suit individual interests.
- Lastly, excess time is consumed because of the several rounds of clarifications and corrections that take place before the final version of CSVSM.
Keep in mind that there is no single approach to overcoming these obstacles to a successful CSVSM. An instructor’s experience of handling such conflicts is the key to helping resolve them. Furthermore, it is useful to print the final version of a CSVSM in a legible format and then paste it on a wall. This helps in making it visual and increases people’s accessibility to posting thoughts on it without having to go to a computer every time. Once a current state value stream map is complete, it is subjected to evaluation.
Basis of Evaluation of a Current State Value Stream Map
- First, it is based on its value to the customer (the end customer).
- Wear the ‘first principle’ lens and classify value-added and non-value-added time.
- Second, it is based on its value to the business enterprise. Consider the following measures of success for every step of the value stream:
- Cost per unit/transaction/step:
- Efficiency
- Productivity – Man and Machine
- Utilization
- Quality/ Rework %
- Cost per unit/transaction/step:
The next two principles of Lean help us understand and identify improvement opportunities in a CSVSM.
Third and Fourth Principles: To establish ‘Flow’ and achieve ‘Pull’
Sreedher: Does anyone wish to share their views on these two terms?
Participants: [silence]
Sreedher: Fine, let me share a real-life example. I stay in a city where traffic congestions are a daily affair. However, I reach my destination reasonably fast when I either travel before 7:00 a.m. or after 11:00 p.m. Do you know why?
Participants: No signals, no stoppages, no policing, and potholes are visible!
[Laughter]
Sreedher: Correct! There’s an uninterrupted flow. Similarly, any work undertaken in an office is a ‘start, stop, start, stop’ affair. To create flow, you should first find out what stops flow? Lean thinking has identified 8 types of flow stoppers. You can remember them as ‘TIMWOOD’:
- Transport
- Inventory
- Motion
- Waiting
- Overproduction
- Over-processing
- Defects
Usually, one waste leads to another. For instance, rework and inventory leads to waiting.
Therefore, when you develop a current state value stream map, you should look for flow stoppers. You may want to leave a ‘star symbol’ where you find them.
Inside the starburst, write your observation of the nature of the waste. Non-value-added steps are barriers to flow, as they consume time and resources without any payoff.
The eighth waste: There is one more type of waste, which is the under utilization of human potential. What does it mean? It refers to the inadequate usage of human resources and intelligence. This is the mother of all wastes! For example, it takes place when employees walk past a non-value-added activity without thinking and acting on it. Hence, it is essentially the cause of all the other wastes.
Lean aims at engendering efficient, fast, and precise process flow, along with its alignment to the customer’s needs. Lean thinking saves resource time by making the workflow simpler and more effective. Therefore, it creates an additional capacity within existing resources. Non-value-added actions are not just limited to manufacturing processes. They exist in non-manufacturing ones as well! Let’s look at such examples:
- Transportation: This involves travelling across a long distance to collect printouts, scanned copies, etc.
- Inventory: This includes files, documents, e-mails, semi finished transactions, and information that are waiting to be addressed and acted upon.
- Motion: This would be when someone says, “I need to reach too far to grab a stapler or a file!”
- Waiting: It occurs when there are files or transactions that remain stagnant at a manager’s desk for approval.
- Overproduction: This happens when 10 files are completed and submitted for the next transaction step, regardless of the speed of the transaction.
- Over-processing: This involves the unnecessary approvals and decision loops that stop data from being acted upon.
- Defects: This occurs when drawings aren’t drafted correctly the first time, incorrect approvals are given, etc.
To summarize, find what stops the flow and then identify how the flow should be established. These ideas are called Kaizens in the Lean world.
Alright, now we come to the next principle, i.e., pull. Does anyone know what it is?
Participants: [Scattered response] Producing to customer demand…
Sreedher: Yes, that’s correct! Pull production is the production of a product to customer demand.
Participants: [Softly] So, those who purchase our products?
Sreedher: Yes. One class of customers is called ‘external customer’, while another is ‘internal customer’. Who are internal customers?
Participants: Next operation.
Sreedher: Perfect! 10 points for the answer. The next operation is the customer. It is like cooking and serving food at home. When the food is cooked, the chef asks, “Do you need some more?” If the answer is ‘yes’, then the preparation continues. If the answer is ‘no’, then it stops. The goal is to ensure that the food is served hot, just in time, and meets the expectations of the one who eats it.
First, identify who your internal customer is. Then ask them:
- What is needed? – Quality
- How much is needed? – Quantity
- When is it needed? – Timeliness
If these 3 criteria are met consistently, you’re likely to have successfully implemented pull production! There are various tools to facilitate its achievement, including Kanban, single-piece flow, cellular manufacturing, etc.
In the example discussed earlier, recollect that we improved the following using Lean:
- First, we ensured that production was right the first time (quality %).
- Second, we improved the quality and timeliness of supplies.
- Third, there was a first time right % of the support roles – such as Design and Development, Sales etc.
- Lastly, regarding the machine-availability on-demand %:
- There was a decrease in changeover times.
- There was a decrease in unplanned downtime.
And what was the target set in each case? 100%!
Now, how long do you wish to stay fit? Forever! Therefore, what non-value-added time you will tolerate?
If you say none, then you are in the pursuit of ‘perfection’ – the fifth Lean principle.
Fifth Principle: Aim for ‘Perfection’
Sreedher: The continuous improvement journey remains alive for as long as you chase perfection. Keeping it as your vision makes the journey enjoyable and results in innumerable benefits. Always remember that extraordinary results are achieved with extraordinary effort.
The phrase that ‘change is constant’ shows us that an FSVSM today becomes a CSVSM tomorrow. Dream big, work hard, and success is bound to follow.