The Lean tool Kanban is “a signal or an instruction to get, move, produce, order, or take an activity with production materials”. It regulates material flow by using signalling cards known as ‘Kanban’ cards. Although the specific information within a Kanban card may vary, most will contain some of the following information:
- Part description
- Part/ item number and/ or an identifying bar code
- The number of parts to be moved/ produced/ ordered
- Routing information/ upstream or downstream processes
- Location information
- Lead time
- Supplier
- The responsible person (e.g., the planner)
- The order dates
- The due date
- Type of container
- Number of containers (i.e., card 2 of 4)
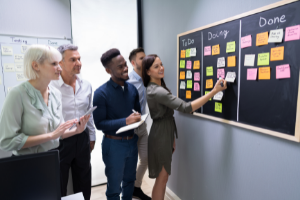
How does a Kanban system work?
The figure below describes how a Kanban system works. A customer withdraws a product from the supermarket using a withdrawal Kanban card. This, in turn, triggers the production to produce and refill the withdrawn quantity in the supermarket.
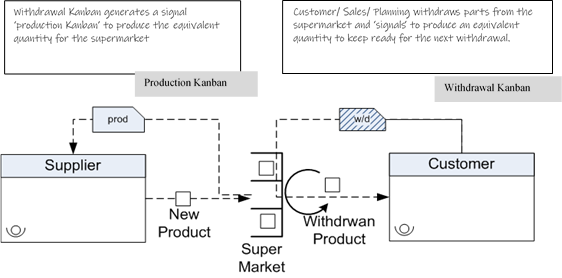
Figure 1 – How a Kanban system works
Rules of Kanban
- A downstream process pulls items from an upstream process.
- Upstream processes produce only what has been withdrawn.
- Send 100% defect-free products to the next process.
- Set up level production.
- Kanban always accompanies the parts.
- Decrease the number of Kanban’s overtime.
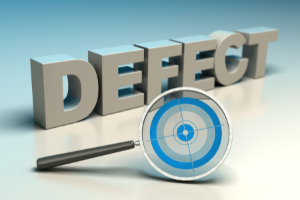
The most critical rule to make Kanban implementation successful is rule 3. Therefore, operators should self-inspect the parts and send only defect-free parts to the next step.
Kanban in Services
To understand its connection to the service sector, look at the following example of Kanban in recruitment:
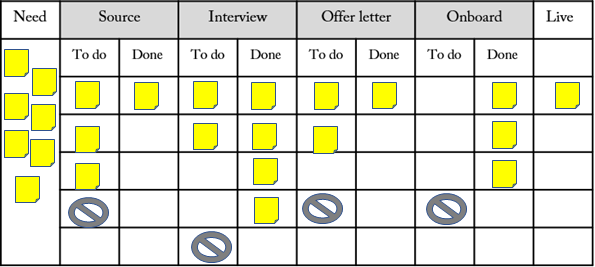
Figure 2 – Kanban in services
Here:
- All recruitment indents are displayed in ‘Need’.
- Source, interview, offer letter and onboard represent recruitment steps.
- ‘To do’ and ‘done’ show the status.
- The ‘no parking’ symbol suggests ‘capacity’. For example, onboard can take up to three more requests. On the other hand, ‘source’ has its hands full.
Prerequisites to Implement Kanban
Kanban enables ‘pull production’. To enable this, you must ensure that these practices are in place:
- 5S
- Load Levelling or Heijunka
- Takt, balance, and flow
- Visual factory
- Material handling systems like forklifts, storage racks, and bins should be in good working condition.
- If you use bar codes to track the material, then you should integrate them into Kanban cards.
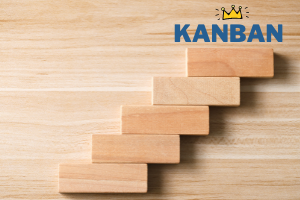
Make to order or make to stock?
While implementing Kanban, it is necessary to identify the strategies most suitable for your business. Hence, this brings in the dilemma of ‘make to order or make to stock’? Therefore, it essentially revolves around push versus pull production. The following guidelines can help you decide:
- Firstly, if variability is high and volume is high – make to stock
- Secondly, when variability is high and volume is low – make to order
- Thirdly, if variability is low and volume is low – make to order
- Lastly, when variability is low and volume is high – make to stock
Use Kanban systems for pull production and strategic inventory. If the demand uncertainty is low, use a push and continuous production model.
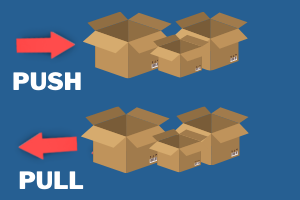