How ERPNext Transformed Cost Tracking for an Agro Product Business
Industry: Agro Product Manufacturing Companies, IT Services
Author: Ramanujan KK
Publish Date: 21 February, 2025
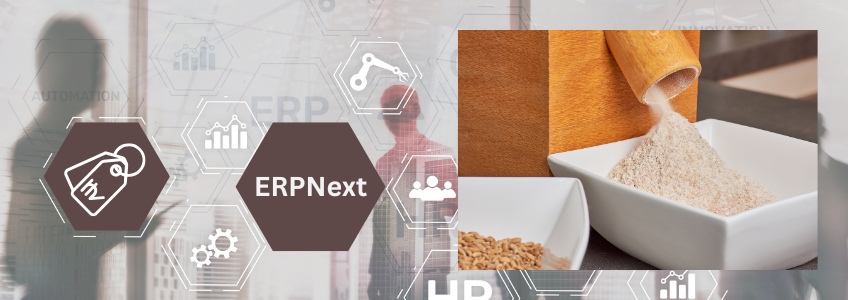
Introduction
An Agro Product Processing Company specializes in the production of refined flour, wheat flour, bran, and granulated wheat flour. They faced difficulties in accurately tracking and verifying the costs associated with their manufacturing processes. The management struggled to determine whether their selling prices were aligned with the true cost of production, often lacking confidence in the accuracy of their pricing strategy.
After implementing ERPNext, the company gained the ability to generate real-time cost reports by process. This ensured precise cost tracking and helped the management confidently set selling prices. This case study highlights how ERPNext transformed the company’s approach to cost management, enabling more accurate pricing and improved profitability.
The Story of the Agro Product Processing Company
The company is a leading producer of flour products, including refined flour, wheat flour, bran, and granulated wheat flour. They have multiple production lines handling different types of wheat processing. Here, the company faced significant challenges in determining the true cost of production for each product.
Although the company had a basic accounting system, it could not track costs by specific processes such as milling, sifting, packaging, and quality control. This lack of detailed visibility led to inaccurate cost estimations and pricing strategies, creating uncertainty about profit margins.
To address these challenges, the company sought a comprehensive solution that could provide real-time cost tracking across each stage of their manufacturing process. After evaluating several options, the company chose ERPNext for its ability to break down costs by process. ERPNext is also able to provide automated, up-to-date financial data.
The Challenge of Cost Tracking and Confidence in Pricing
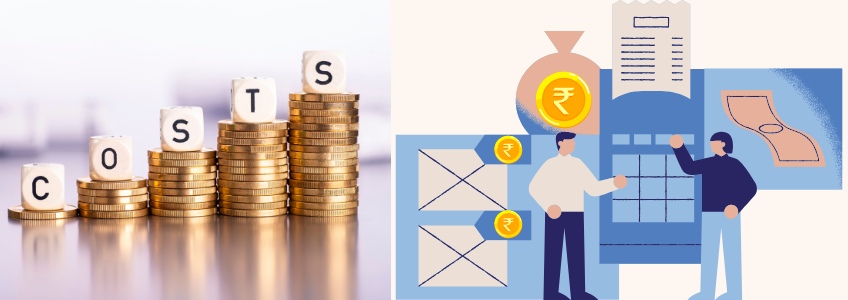
Before implementing ERPNext, the Agro Product Processing Company faced several key challenges.
- Difficulty in Breaking Down Costs by Process:
The company could not effectively track costs by individual processes such as milling, sifting, and packaging. While they had access to overall cost data, they couldn’t determine the true cost of producing each specific product (refined flour, wheat flour, bran, etc.). - Uncertainty About Selling Prices:
Due to a lack of visibility into the actual production costs, management had difficulty verifying whether their selling prices were competitive and aligned with the cost of production. This uncertainty often led to concerns about whether they were making the right margin on each product. - Inefficient Cost Calculation:
The manual process of calculating production costs was time-consuming and error-prone. It was difficult to account for fluctuating costs of raw materials (wheat), labor, energy consumption, and overheads in real time, causing delays in updating pricing and financial projections. - Profitability Concerns:
Without the ability to break down costs into smaller components, the company struggled to determine which products were most profitable and where cost optimization was possible. As a result, some products may have been underpriced, eroding profits.
How the Agro Product Processing Company Used ERPNext
Once ERPNext was implemented, the company followed the steps, listed below, to track manufacturing costs across each process involved in flour production.
- Cost Reports by Production Process:
ERPNext allowed the company to track costs by individual production processes, including milling, sifting, granulation, and packaging. The system generated real-time reports on material costs, labor costs, overhead costs, and energy consumption for each process. This breakdown provided management with a granular view of how costs were distributed across each stage of production. - Real-Time Data Integration:
As raw materials like wheat were consumed, labor hours logged, and energy usage recorded, the data was automatically updated in ERPNext. This real-time integration allowed management to quickly access the latest cost data and adjust pricing accordingly. - Custom Cost Allocation:
ERPNext allowed the company to customize cost allocation rules, ensuring that each product (refined flour, wheat flour, bran, etc.) received a fair share of the overhead costs based on its respective production process. This helped ensure that the cost of manufacturing each product was accurate and reflective of the actual resources used. - Profitability Analysis:
Using the cost reports generated by ERPNext, the company was able to analyze the profitability of individual products. By comparing the cost of production with the selling price, management could identify underpriced products and adjust accordingly to improve
The Results
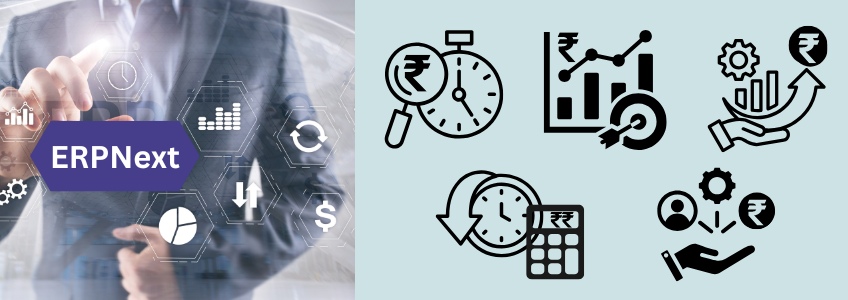
The implementation of ERPNext led to several key improvements in the company’s cost-tracking and pricing strategy.
- Improved Cost Tracking by Process:
The company now could track costs in real time across different production processes. This granular approach helped the company optimize its manufacturing workflow and reduce inefficiencies in production. - Increased Confidence in Pricing:
With accurate cost data, management could confidently set selling prices for each product, knowing that their prices were aligned with the true cost of production. This significantly increased their confidence in their pricing strategy. - Optimized Profit Margins:
By using detailed cost reports to understand the profitability of individual products, the company was able to adjust selling prices and increase its profit margins. Some products that were underpriced were brought in line with the actual cost of manufacturing, improving overall profitability. - Reduced Time Spent on Cost Calculation:
The automated cost reporting process reduced the time spent on manual calculations by 50%. This not only improved operational efficiency but also freed up resources for other critical tasks in the company. - Better Resource Allocation:
Real-time cost tracking helped the company identify areas where resources (e.g., labor, raw materials) were being over-utilized. This insight allowed for better resource allocation and waste reduction, leading to cost savings.
The ability to track costs at each stage of production in real-time has been invaluable. ERPNext has given us the tools to make better pricing decisions and ensure we’re always on track for profitability.” – Production Manager, Agro Product Processing Company
Conclusion
The Agro Product Processing Company gained accurate, granular insights into its production costs by implementing ERPNext for real-time cost tracking. This empowered management to make data-driven pricing decisions, improved profitability and increased confidence in their pricing strategy.
ERPNext’s ability to track costs by process also ensured that each product was accurately priced, reducing pricing uncertainty and boosting the company’s bottom line.
If you are interested to achieve similar success stories, write to us!