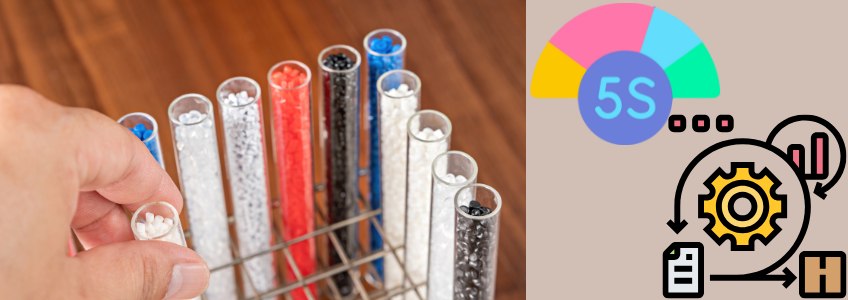
Introduction
To thrive in the competitive landscape of the polymer industry, encompassing the production of plastics, rubbers, and other synthetic materials, companies must prioritize efficiency, quality, and safety. The 5S methodology, a lean manufacturing principle originating in Japan, offers a powerful framework for achieving these goals.
This blog post will explain in detail the significance of 5S in the polymer industry, exploring its benefits and practical implementation strategies.
What is 5S?
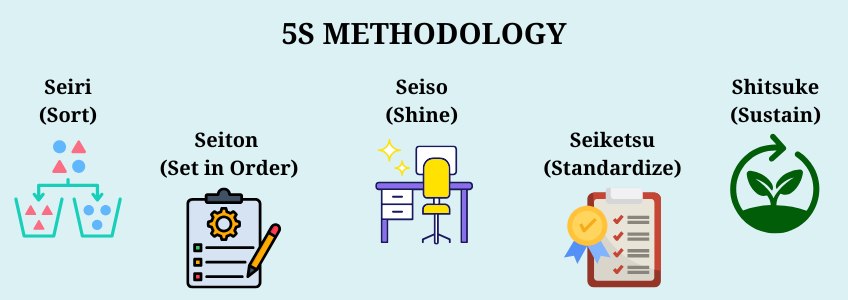
5S is an acronym representing five Japanese words:
1. Seiri (Sort)
- Identify and remove unnecessary items from the workplace.
- Clearly distinguish between necessary and unnecessary items.
- Involve employees while making decisions.
2. Seiton (Set in Order)
- Arrange and organize necessary items for easy access and efficient use.
- Assign a specific location for each item.
- Ensure that items are stored in a way that prevents damage and facilitates efficient retrieval.
3. Seiso (Shine)
- Keep the workplace clean and free from dust, debris, and spills.
- Establish a regular cleaning schedule and assign responsibilities.
- Identify and address the root causes of dirt and clutter.
4. Seiketsu (Standardize)
- Maintain order and cleanliness consistently through standardized practices and visual controls.
- Use visual controls to ensure that standards are being met.
- Conduct regular audits to identify and address any deviations from standards.
5. Shitsuke (Sustain)
- Cultivate a culture of continuous improvement by maintaining 5S principles over the long term.
- Celebrate successes and recognize employee contributions.
- Regularly review and update 5S practices to adapt to changing needs.
Benefits of 5S in the Polymer Industry
The implementation of 5S principles can yield significant benefits for polymer manufacturers.
1. Enhanced Safety
- A clean and organized workspace minimizes tripping hazards. It reduces the risk of slips and falls, and improves visibility, thereby enhancing overall safety. For instance, clearly marked walkways and designated storage areas for materials can prevent accidents.
- Regular cleaning and maintenance of machinery prevent accidents and ensure optimal equipment performance. For example, removing oil spills and ensuring proper lubrication can prevent fires and equipment malfunctions.
- A well-organized workspace minimizes the risk of musculoskeletal disorders (MSDs) among employees by ensuring ergonomic workstations and easy access to tools and materials.
2. Improved Quality
- A clean and organized workplace reduces the risk of contamination. It ensures that materials are handled and processed correctly, leading to a reduction in product defects. For instance, maintaining cleanliness in injection molding machines can prevent contamination of molten plastic, resulting in higher quality parts.
- Standardized procedures and visual controls ensure consistent product quality and minimize variations. For example, color-coding materials and implementing visual controls for process parameters can help maintain consistent product characteristics.
- By consistently delivering high-quality products, 5S contributes to increased customer satisfaction and improved brand reputation.
3. Increased Efficiency
- By identifying and eliminating unnecessary items, 5S helps to minimize waste in materials, energy, and time. For example, implementing a “first-in, first-out” system for inventory can reduce the risk of material spoilage and minimize waste.
- A well-organized workspace facilitates smooth and efficient workflows, minimizing bottlenecks and delays. For instance, clearly defined work areas and designated storage locations for tools and materials can streamline production processes.
- By reducing waste and improving efficiency, 5S can significantly boost overall productivity by even 20-30%.
4. Cost Savings
- Regular maintenance and proactive issue identification reduce equipment downtime and costly repairs. Regular cleaning and inspection of machinery can identify potential problems early on, preventing costly breakdowns.
- Minimizing waste in materials and energy translates into significant cost savings. Reducing scrap rates and optimizing energy consumption can lead to substantial cost reductions.
- Efficient organization of inventory reduces stockouts and minimizes the risk of damage or spoilage. For example, implementing a visual inventory system can help to track inventory levels accurately and minimize the risk of overstocking.
5. Boosted Morale
- A clean and organized work environment can boost employee morale and motivation.
- Employees feel more comfortable and productive in a well-maintained workspace.
- 5S empowers employees to take ownership of their workspace and contribute to continuous improvement.
- Employee involvement in the 5S implementation process can increase their sense of ownership and pride in their work.
6. Team Engagement
- One of the key aspects of implementing 5S successfully is engaging the team and building up a sense of responsibility amongst the people on the production floor.
- The team should feel not only responsible but also accountable for their actions.
- The team needs to be motivated towards 5S and must be appreciated for their dedication and efforts in sustaining the 5S. This will make them feel a valued member of the company.
- Sustaining 5S is one of the biggest challenges faced by the companies and it can only be achieved if every person in the company is committed towards it.
Conclusion
Polymer manufacturers can create a safer, more efficient, and more productive work environment, by effectively implementing 5S principles. The benefits of 5S extend beyond improved safety and efficiency, encompassing enhanced quality, reduced costs, and increased employee morale.
Therefore, by fostering a culture of continuous improvement and employee engagement, 5S can drive significant competitive advantage in the dynamic polymer industry.
If you are interested to achieve similar success stories, write to us!