The 5S is a Japanese approach to ‘workplace discipline’. Each ‘S’ represents a Japanese term and a subsequent step to organize any workplace. There are 5 simple steps of the 5S principles:
- Sort
- Set in order
- Shine
- Standardize
- Sustain
What does the 5S Approach do?
You can understand the applicability of the 5S approach by an example from our daily life. Imagine that you reach home after a hard day’s work at the office. You find your house to be sparkling clean and tidy. Everything is in its place. How did you feel? On the contrary, how would you feel if you find that the objects are not in their place? What if they were all kept haphazardly?
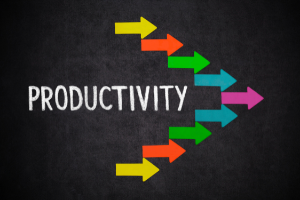
5S isn’t rocket science. It is a simple, yet effective technique to be productive at work or home. If you wish to carry out Lean implementation at your workplace, 5S is a perfect starting point. It will engage everyone in the plant to design their workplace in the best way possible! The key to the 5S approach is to carry out one step at a time.
How much time does each step of the 5S approach take?
It depends on the commitment and eagerness of the people to the 5S approach. Furthermore, it depends on the sense of urgency to achieve the best looking, feeling, and productive workplace. Additionally, it depends on how messy your current state is!
Below are some pictures from places where I carried out a 5S initiative.
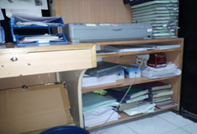
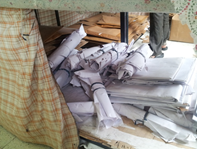
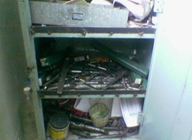
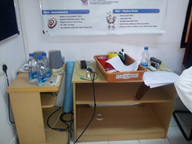
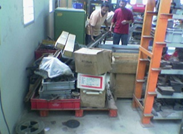
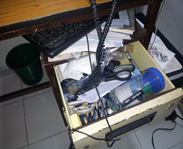
Figure 1 – Workplace picture before 5S and sorting
Therefore, it is crucial to carry out the 5S approach to reach optimal workplace organization!