The 5 Whys analysis (or why–why analysis) is a Lean tool and is one of the most powerful techniques to discover the root cause of any problem. It repeatedly asks why something has happened till the source of the issue is identified. However, remember that different cases may have different root causes. Therefore, it is important to perform a 5 Whys analysis on a case-to-case basis.
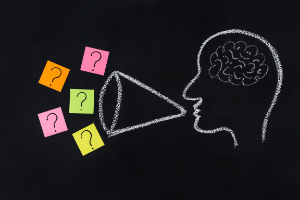
To understand the 5 Whys analysis, consider this example: In a warehouse, there is a delay in vendor payments. A sample of 140 cases suggests that the primary reason for the delay in vendor payments is ‘incorrect vendor name’. The chart below is a Pareto diagram. It is also known as an 80-20 rule diagram, whereby 80% of the problems is caused by 20% of the reasons. Pareto diagrams are useful to identify and prioritize the top causes of problems.
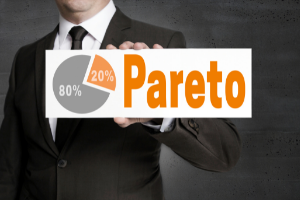
In the Pareto diagram below, notice how ‘incorrect vendor name’ poses as 44% of the overall reasons. Additionally, in this case, there are 140 cases of ‘incorrect vendor names’. Therefore, use a Pareto diagram to prioritize the reasons behind further investigations.
How Can I Carry Out a 5 Whys Analysis?
To perform a 5 Whys analysis, it is important to consider one case at a time. To examine the root cause of a problem while an incident takes place is far easier rather than finding it afterwards. Hence, this technique is most effective when carried out while the concerned event occurs!
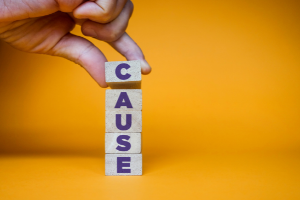
For a deeper understanding of how you can perform a 5 Whys analysis, let us branch out from the case mentioned above. Consider just one of the 140 cases. Firstly, you need to ask why: Why was the vendor’s name wrong? Based on the answer that you receive, ask yourself if you need to ask another why question. Most importantly, use your judgment in this case! Once you see that you cannot go any further, stop the why-why analysis right here!
Here’s an example of how you should go about the 5 Whys analysis:
Find the Root Cause:
- Firstly, why was the wrong vendor name mentioned here?
Answer: The wrong vendor name was fed into the system.
- Secondly, why was the vendor’s name wrong in the system?
Answer: Wrong data entry.
- Thirdly, why did the operator enter incorrect data?
Answer: They used the name as found in the vendor application form. However, the operator must refer to the PAN card for a vendor’s name.
- Fourthly, why didn’t the operator use the PAN card for referring to the vendor’s name?
Answer: They didn’t know. Perhaps the operator was a newcomer and was put on duty the same day he joined. Hence, with little training and almost no work instructions, mistakes may occur.
Therefore, there are 2 root causes of the problem in this scenario:
- Recruit inadequately trained.
- Work instructions do not specify ‘use PAN card to enter vendor name’.
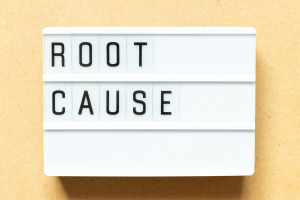
Identify the Corrective and Preventive Actions:
The next plan of action in a 5 Whys analysis is to identify the corrective and preventive actions. Additionally, identify who is accountable for this as well as when they should carry out the solutions by. Use data and direct evidence from the shop floor to validate answers to every ‘why’. One common mistake people do is to put ‘assumed answers’ to each of these ‘whys’. However, in such cases, you’ll be lucky if you get to the root cause!
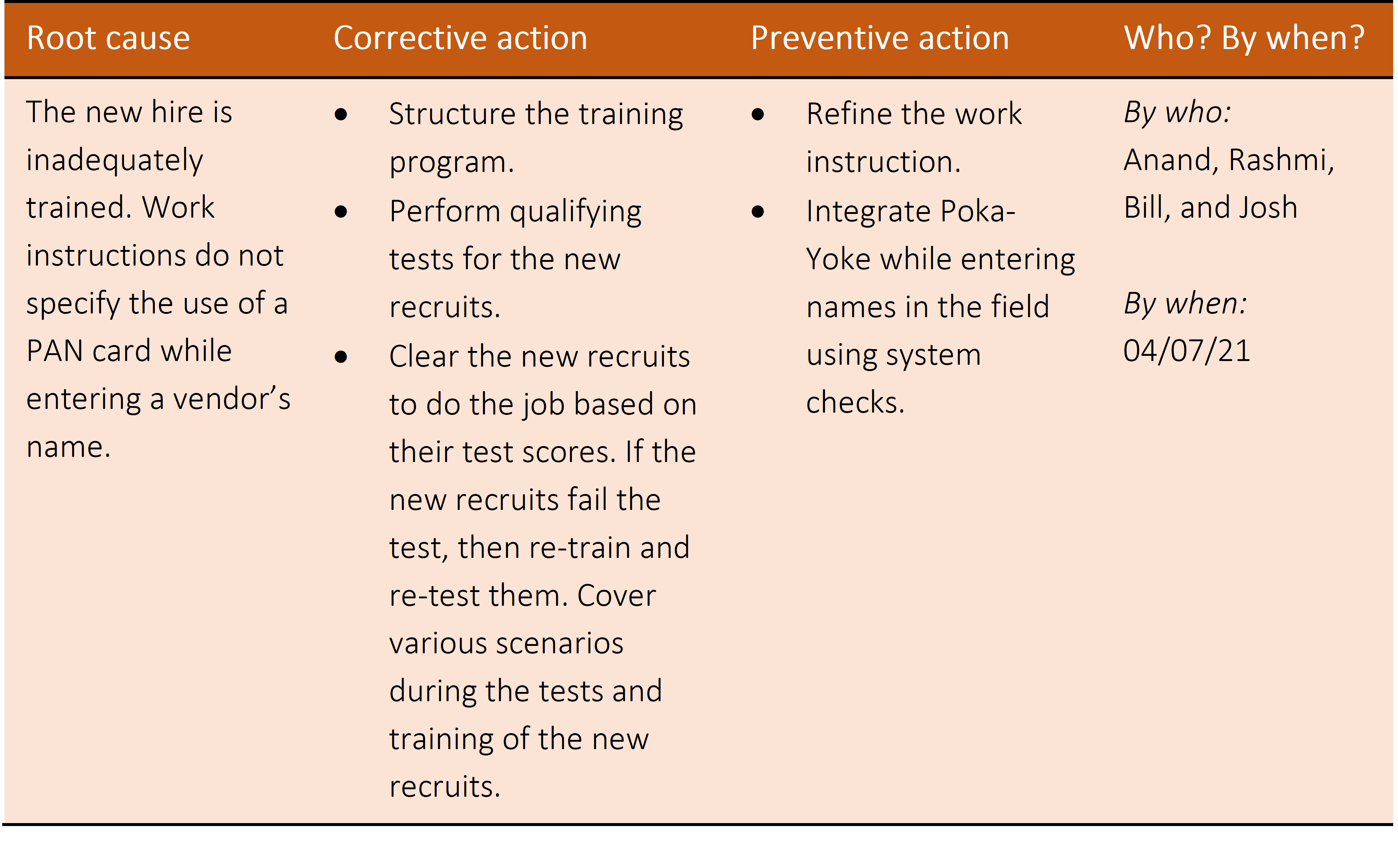